bugbus
Structural
- Aug 14, 2018
- 515
What is the failure mode for a bracket like this? I imagine it is more complicated than it appears, and probably involves some kind of twisting action.
I wonder if there are any design guides or if anyone has prior experience?
I wonder if there are any design guides or if anyone has prior experience?
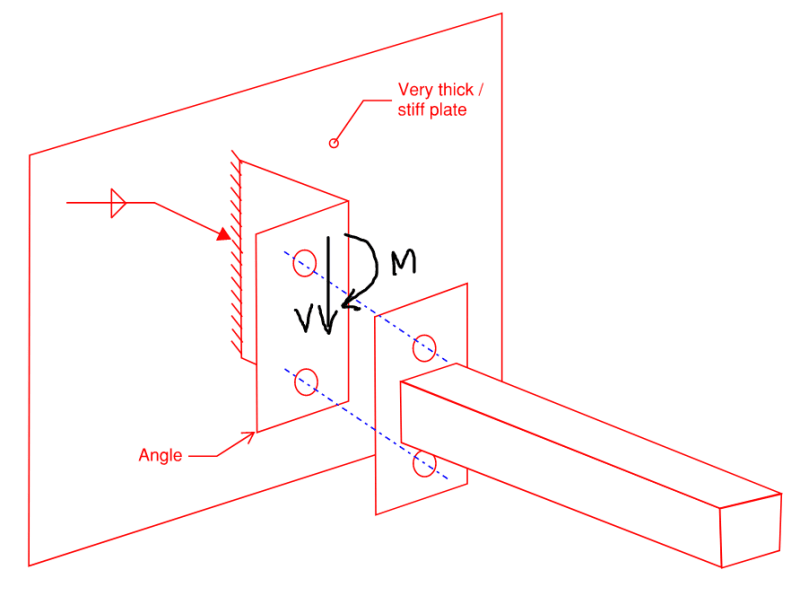