EagerOne
Student
- Nov 20, 2023
- 4
Hi All,
I am a student who is trying to do something new for a change. This is not yet in my course material but just interested in learning. I was reading about how vaulted ceilings can be framed and came across this article ( which shows how a steel plate is used as a component in a flitch beam scenario. This allows the contractor/designer avoid collar or rafter ties and also avoids a ridge beam.
I have done very few welding design activities beyond the basics. I understand that I have to model the "a-frame" rafter assembly to find the moment at the peak (completed), and then design the welded connection of the two plates to sustain this moment.
Does anyone have any tips on how to complete this weld design?
Thank you.
I am a student who is trying to do something new for a change. This is not yet in my course material but just interested in learning. I was reading about how vaulted ceilings can be framed and came across this article ( which shows how a steel plate is used as a component in a flitch beam scenario. This allows the contractor/designer avoid collar or rafter ties and also avoids a ridge beam.
I have done very few welding design activities beyond the basics. I understand that I have to model the "a-frame" rafter assembly to find the moment at the peak (completed), and then design the welded connection of the two plates to sustain this moment.
Does anyone have any tips on how to complete this weld design?
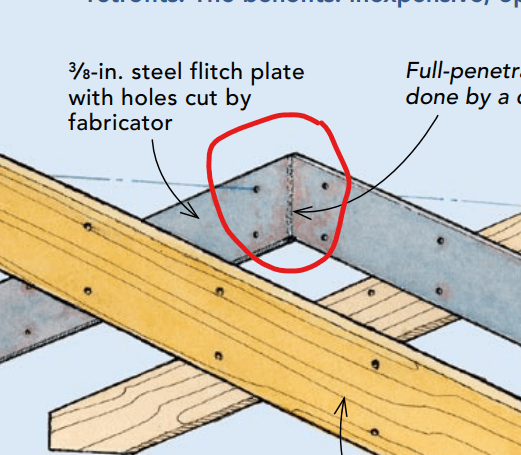
Thank you.