pinaki_stahlbau
Civil/Environmental
- Dec 11, 2024
- 4
Hello,
I am working on a construction project in Europe and the fabricators have proposed a T joint, where in the 3rd member sits on an existing groove joint. The idea is that the groove joint will be first formed and inspected thoroughly for any defects and then the thinner plate comes and sits on the existing weld metal.
My questions is if this is valid and if any special checks need to be carried out. If such a thing is indeed okayed by any norm or book, could you direct me to one.
Thanks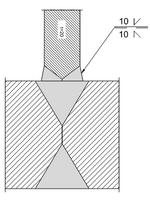
I am working on a construction project in Europe and the fabricators have proposed a T joint, where in the 3rd member sits on an existing groove joint. The idea is that the groove joint will be first formed and inspected thoroughly for any defects and then the thinner plate comes and sits on the existing weld metal.
My questions is if this is valid and if any special checks need to be carried out. If such a thing is indeed okayed by any norm or book, could you direct me to one.
Thanks
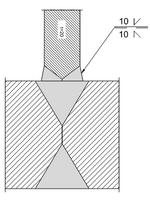