Mechanical guy
Mechanical
- Jun 22, 2019
- 11
Hi all ,
i have a problem in one of our Plant centrifugal blowers , when it was stopped it gave a HH alarm for axial displacement.
can anyone help me to know what could be the root cause for this problem ??
The blower was offline for around 1.5 months for some low lube oil pressure then oil issues solved by operation team but when they start the blower the HH alarm for axial displacement came up.
the blower was stopped and we rotated the blower by hand and the alarm was reduced from high high to high only. ( from > + 0,55 mm reduced to > + 0,5 mm )but that's it , we need to reduce it more but we don't know what can we do further ,
if you can give me some hints of what can i check or do to solve this i would really appreciate it ,,,,,,,
many thanks in advance ,,,
i have a problem in one of our Plant centrifugal blowers , when it was stopped it gave a HH alarm for axial displacement.
can anyone help me to know what could be the root cause for this problem ??
The blower was offline for around 1.5 months for some low lube oil pressure then oil issues solved by operation team but when they start the blower the HH alarm for axial displacement came up.
the blower was stopped and we rotated the blower by hand and the alarm was reduced from high high to high only. ( from > + 0,55 mm reduced to > + 0,5 mm )but that's it , we need to reduce it more but we don't know what can we do further ,
if you can give me some hints of what can i check or do to solve this i would really appreciate it ,,,,,,,
many thanks in advance ,,,
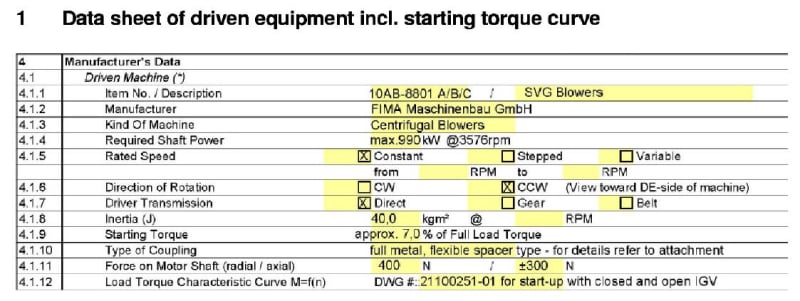
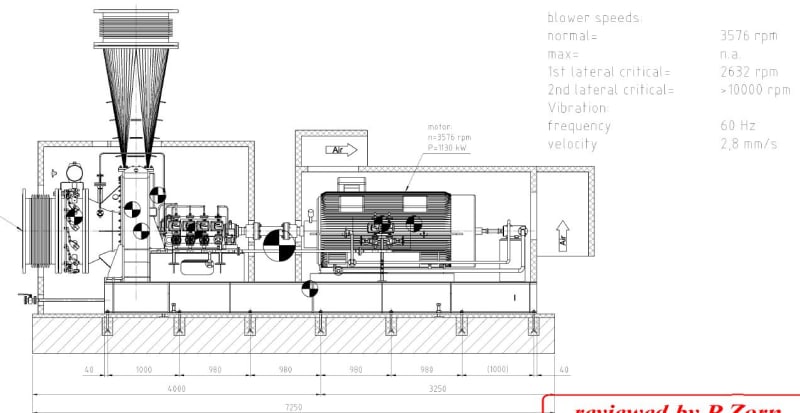