QBlade has submodules named "Rotor BEM Simulation" and "HAWT BEM Simulation". In both of these submodules, they can provide a "lift coefficient vs angle of attack" plot for every wind speed/TSR.
These Cl vs alpha plots are different than the one produced by XFOIL. In fact, I have never seen a Cl vs alpha plot like the one produced by the BEM simulation submodule.
I understand that lift coefficients will change when the turbine is rotating (as opposed to the stationary airfoil used in XFOIL simulations), but I still have never seen such plots.... and I do not understand how or using which method QBlade calculates them.
Does anyone know the name of the theory for which QBlade use in order to create a "lift coefficient vs angle of attack" plot like the picture below? Or at least where can I read about them? I read Robert Gasch and Jochen Twele's book on Wind Power Plants but I do not find any info about producing these plots.
These Cl vs alpha plots are different than the one produced by XFOIL. In fact, I have never seen a Cl vs alpha plot like the one produced by the BEM simulation submodule.
I understand that lift coefficients will change when the turbine is rotating (as opposed to the stationary airfoil used in XFOIL simulations), but I still have never seen such plots.... and I do not understand how or using which method QBlade calculates them.
Does anyone know the name of the theory for which QBlade use in order to create a "lift coefficient vs angle of attack" plot like the picture below? Or at least where can I read about them? I read Robert Gasch and Jochen Twele's book on Wind Power Plants but I do not find any info about producing these plots.
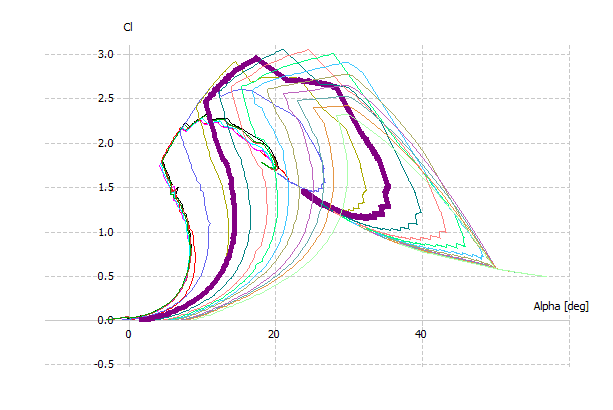