StrucDesignPE
Structural
- Dec 19, 2014
- 110
What type of weld would you specify at this location? Flare Bevel? Fillet? Fill in the gap at the beginning of the HSS radius and then weld? WT is not movable. This is simple shear connection of WF beam to HSS column with e=3". Small 10k load. Figure 8-13 in the AISC manual requires a minimum shelf distance for a fillet weld which is not provided at either side of the WT flange so I don't think I should use a fillet weld, but there really is no radius for a flare bevel to fill. The size of the WT flange in relation to the column width cannot be changed to be larger than or smaller than the column.
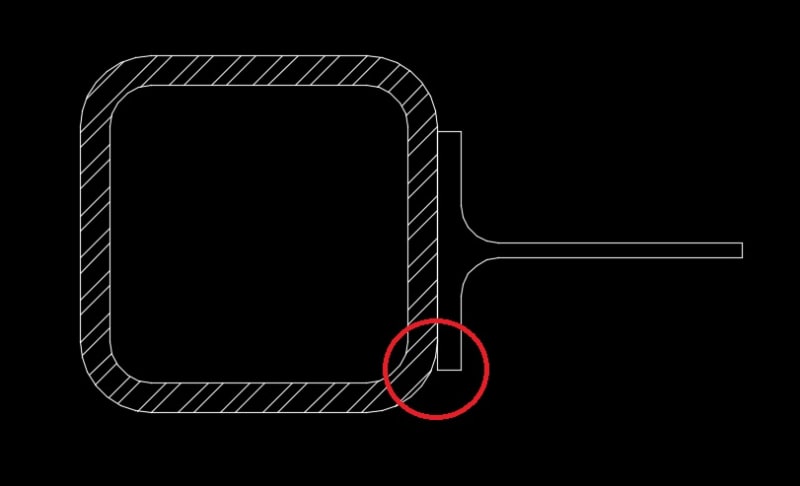