rollingcloud
Aerospace
- Aug 9, 2022
- 174
I have never done any brazing. Our vendor in America is having issues brazing a 321 SS half sleeve onto a 321 SS tube. The tube OD is about .375''. They have a large fallout due to incomplete brazing. The gap tolerance between the sleeves and the tube is .001 - .014''. The sleeve ID is .190 - .200'', it's a standard part. The filler material is Silver Alloy (54Ag - 40Cu - 5.0Zn - 1.0Ni). From the photo, is the gap too large for the capillary action to move the molten filler metal through the joint?
Also, the machining upper tolerance limit of .014'' appear to be too large, I believe .005'' is ideal and .010'' should be the max? Can someone confirm?
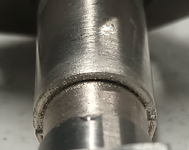
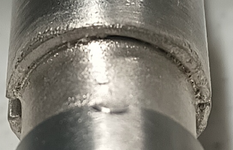
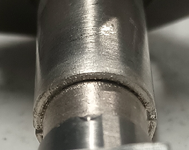
Also, the machining upper tolerance limit of .014'' appear to be too large, I believe .005'' is ideal and .010'' should be the max? Can someone confirm?
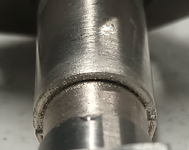
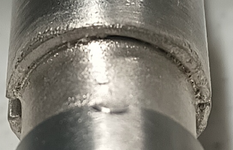
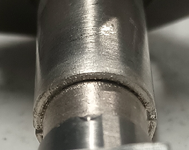
Last edited: