Hello,
I’m struggling trying to model a connector. What I want is to give it specific elastic-plastic behaviors in the three motion directions regardless the rotations, so that if one end point is moved away from the other in direction 1, the connector activates its “1” elastic-plastic behavior, same for direction 2 and 3.
In my model, the first point is coupled to a surface of one 3D element and the other belongs to another 3D element’s face.
What I tried so far, after several attempts, is to create a reference point coupled to the first surface (RF1), then create a connector (join+align) linked to a second coincident point (RF2) that is the first point of the “real” connector, the one I am asking help for and that I modeled as Cartesian at the moment.
The problem I am facing is that when the second element moves, the coordinate system of the connector rotates with the connector, so the effective degree of freedom activated is the one along the connector, not the one in the direction of motion. I uploaded few images to help you understand what I wrote here. Thank you very much.
I’m struggling trying to model a connector. What I want is to give it specific elastic-plastic behaviors in the three motion directions regardless the rotations, so that if one end point is moved away from the other in direction 1, the connector activates its “1” elastic-plastic behavior, same for direction 2 and 3.
In my model, the first point is coupled to a surface of one 3D element and the other belongs to another 3D element’s face.
What I tried so far, after several attempts, is to create a reference point coupled to the first surface (RF1), then create a connector (join+align) linked to a second coincident point (RF2) that is the first point of the “real” connector, the one I am asking help for and that I modeled as Cartesian at the moment.
The problem I am facing is that when the second element moves, the coordinate system of the connector rotates with the connector, so the effective degree of freedom activated is the one along the connector, not the one in the direction of motion. I uploaded few images to help you understand what I wrote here. Thank you very much.
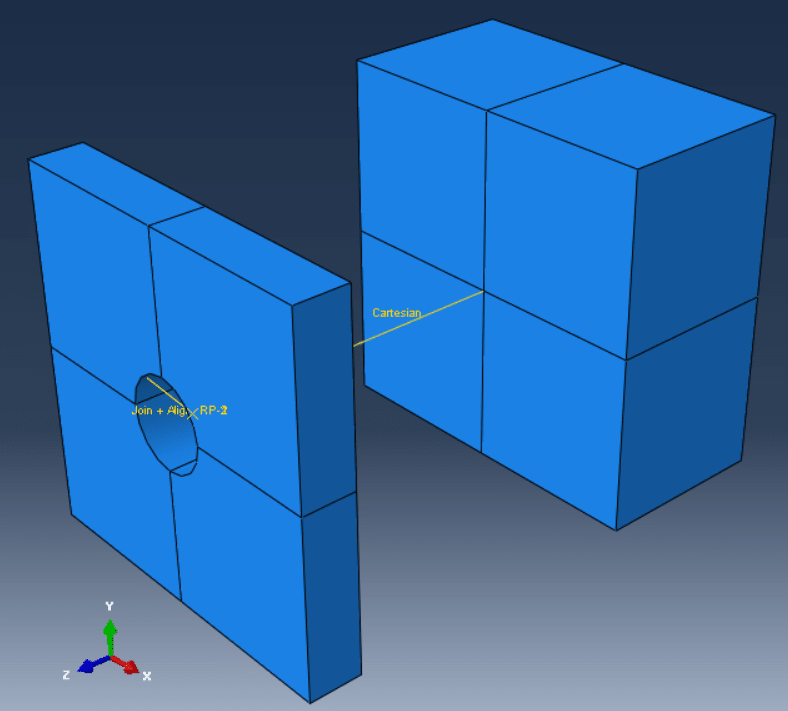
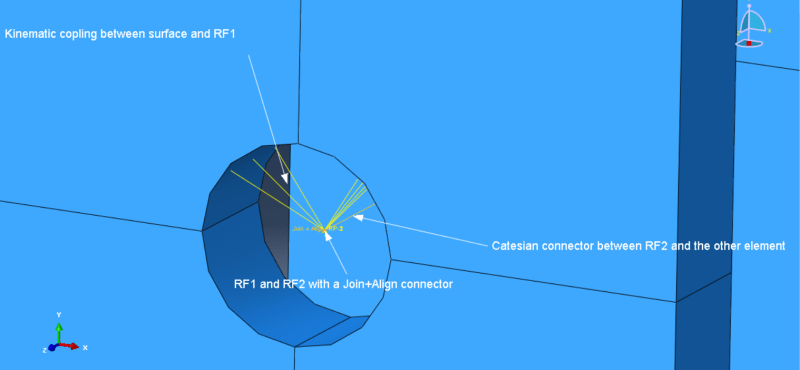
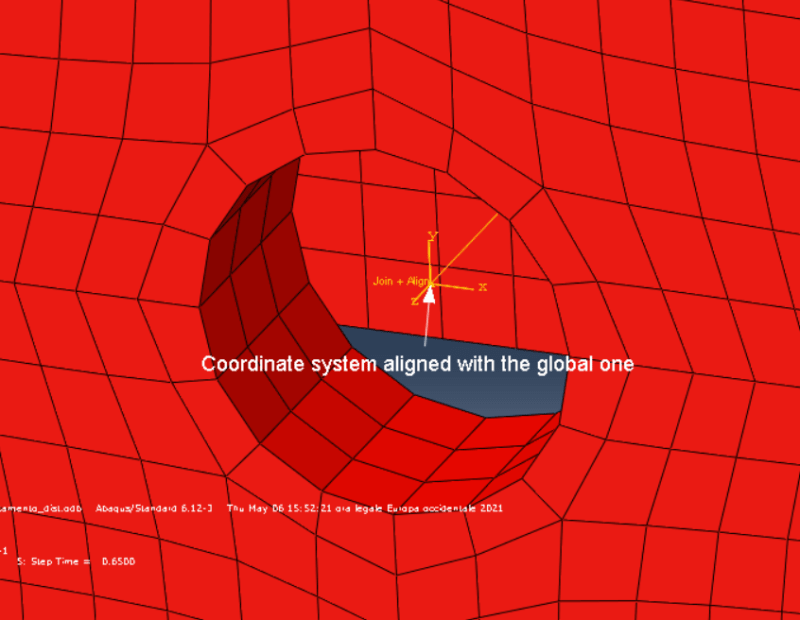
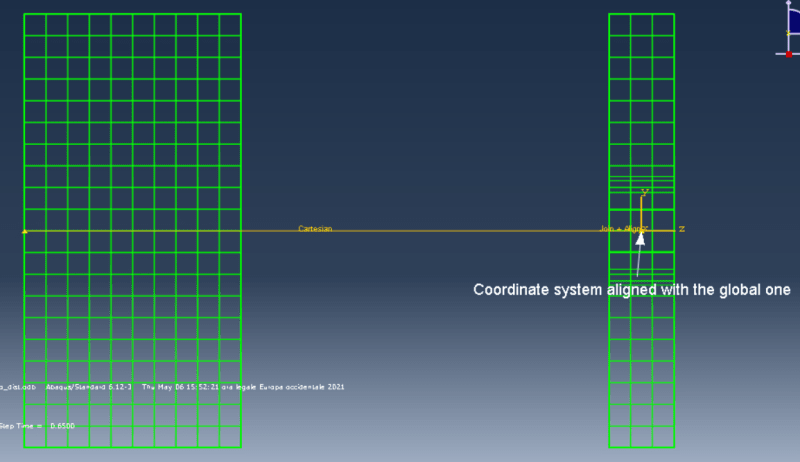
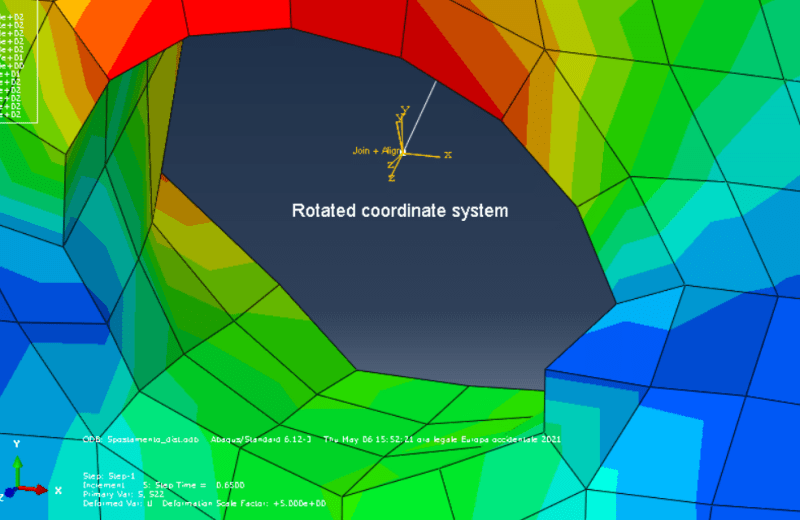
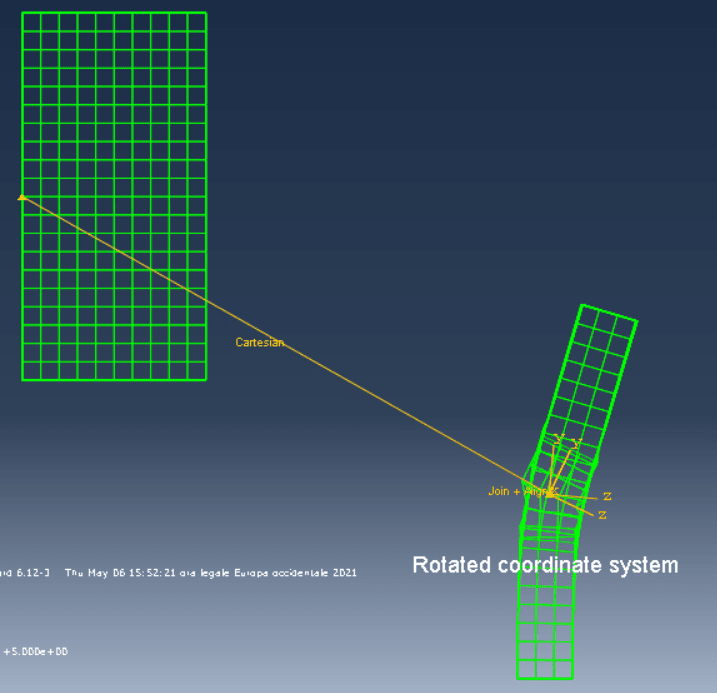