A landlord owns several large warehouses in my area, with long-term tenants. The landlord keeps the buildings in good shape, and is proactive in upgrading and maintaining the roofs, wall envelope etc.
He recently upgraded the roof drainage system, providing new 6" Ø PVC pipes to remove roof gutter water, and routed the vertical pipes through the warehouse and then laterally through the two perimeter internal PEMB tapered steel columns.
For some reason (money I assume) he hired the local 'butcher' and not the local experienced fabricator, who proceeded to use a 5" grinder to cut a 8.5" ø hole in the web of the column, so as to install a pipe-segment reinforcement which was to be welded to the web after installation.
The hack-job resulted in gaps of 1"+ around the scribed 'cut', as follows:
A welder he is NOT!
He recently upgraded the roof drainage system, providing new 6" Ø PVC pipes to remove roof gutter water, and routed the vertical pipes through the warehouse and then laterally through the two perimeter internal PEMB tapered steel columns.
For some reason (money I assume) he hired the local 'butcher' and not the local experienced fabricator, who proceeded to use a 5" grinder to cut a 8.5" ø hole in the web of the column, so as to install a pipe-segment reinforcement which was to be welded to the web after installation.
The hack-job resulted in gaps of 1"+ around the scribed 'cut', as follows:
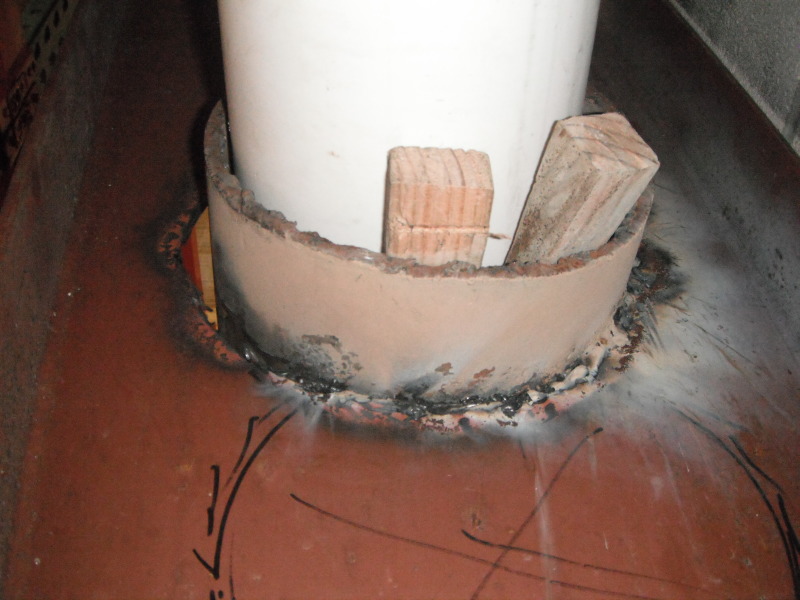
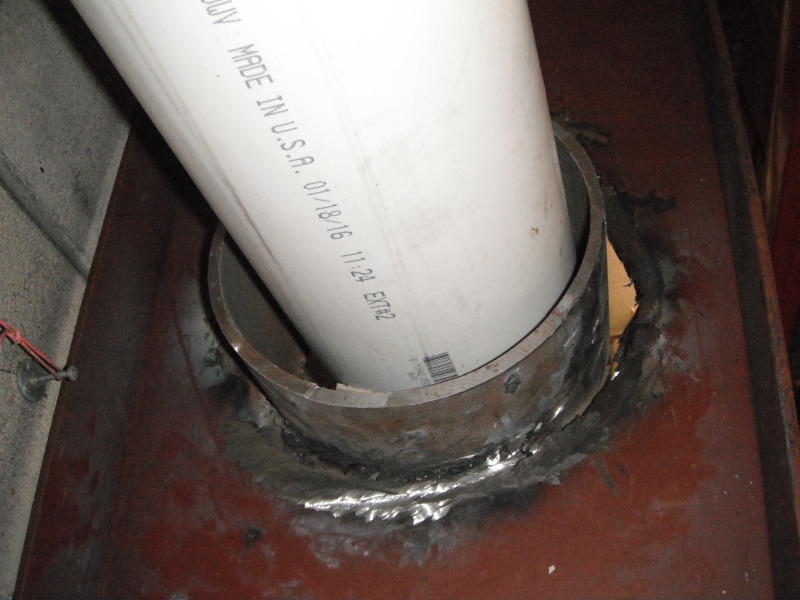
A welder he is NOT!