Hi Experts,
I have to choose pipe welded or seamless for raw gas but it's for 10 to 15 years not more than that, its API 5L X42 fluid is corrosive, no high temperature and pressure. I am looking for any reference from any standard which tells when to use welded and seamless or at least some valid technical points to defend my selection.
Thanks in advance.
I have to choose pipe welded or seamless for raw gas but it's for 10 to 15 years not more than that, its API 5L X42 fluid is corrosive, no high temperature and pressure. I am looking for any reference from any standard which tells when to use welded and seamless or at least some valid technical points to defend my selection.
Thanks in advance.
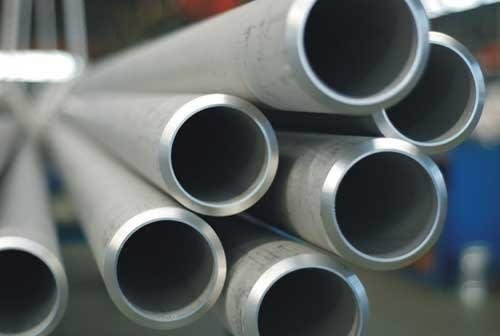