see_gen_notes
Civil/Environmental
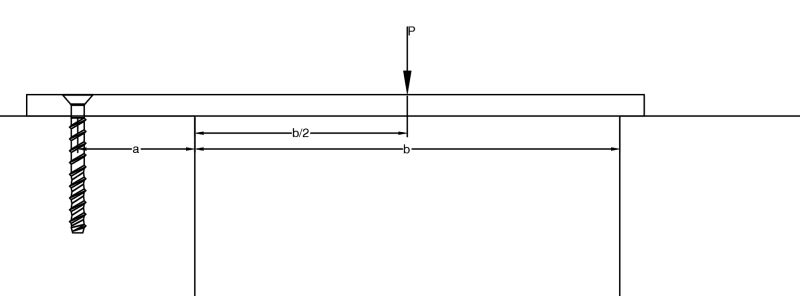
I've been following some old calculations to determine the tension load on the anchor but now I'm second guessing on weather this is really right. Previously the tension load for image was determined based on the free body:
1) [Fixed] --- b --- [PIN]
where the moment was found and divided by ---a--- for the tension load
Now what I think it should be is:
2) [PIN] --- a --- [ROLLER] --- b --- [ROLLER]
The tension load would be the reaction at the pin.
Method 1 gives you a much smaller load while method 2 is larger. Which method to you makes more sense? Or is there another way I should look at it?
Edit: Method 1 actually did give me the larger load, I supiedly forgot to change units as I was doing the checks. I'm going with method 1 as it as more consevative and the loads are still managable.