Hello everyone. I have some doubts about modelling in ABAQUS 6.14 a connection between a wire beam and a solid element (the other part of the beam, where I need to have a more accurate response):
Which kind of constraint could I use? I was thinking to give a coupling between the face of the soild beam and the external point of the wire, but I don't know if that's the right choice. Thanks in advance.
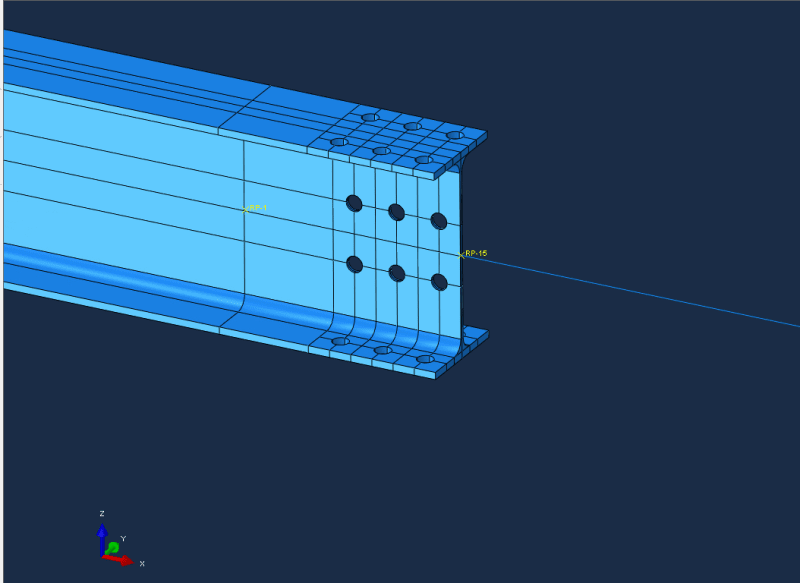
Which kind of constraint could I use? I was thinking to give a coupling between the face of the soild beam and the external point of the wire, but I don't know if that's the right choice. Thanks in advance.