Hello,
I do not know the history of this job that I am now tasked with and the basic information I have is that "someone" installed the drive wired it up and then said it was not the right one.
This is a mixing application that is operating with the motor and gearbox in the pictures DOL with one problem, it is to fast; in certain situation and products. They may start fast and after the product is cooked/ready they slow it down. The products vary very liquid to much thicker and I hear they plan to mix some sort of tomato paste.
230VAC three phase power supply.
5.6 A Motor FLA
Drive output 7 Amps
Let's say the slowest the motor will run is at 30 Hz. ( I have to check motor specs for cooling requirements)
What would be other issues that I may be missing that would make this drive unsuitable?
I am still reading about its Vector Torque mode to find out what it does.
Thanks
I do not know the history of this job that I am now tasked with and the basic information I have is that "someone" installed the drive wired it up and then said it was not the right one.
This is a mixing application that is operating with the motor and gearbox in the pictures DOL with one problem, it is to fast; in certain situation and products. They may start fast and after the product is cooked/ready they slow it down. The products vary very liquid to much thicker and I hear they plan to mix some sort of tomato paste.
230VAC three phase power supply.
5.6 A Motor FLA
Drive output 7 Amps
Let's say the slowest the motor will run is at 30 Hz. ( I have to check motor specs for cooling requirements)
What would be other issues that I may be missing that would make this drive unsuitable?
I am still reading about its Vector Torque mode to find out what it does.
Thanks
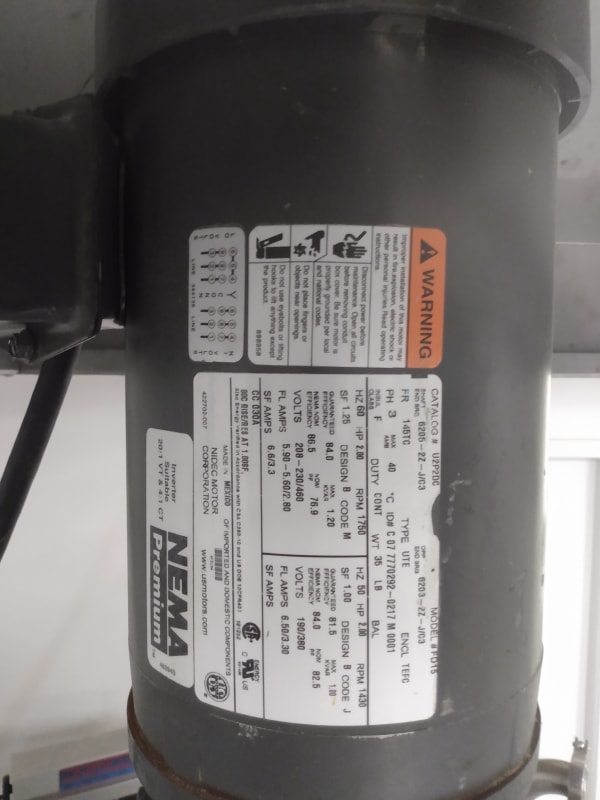
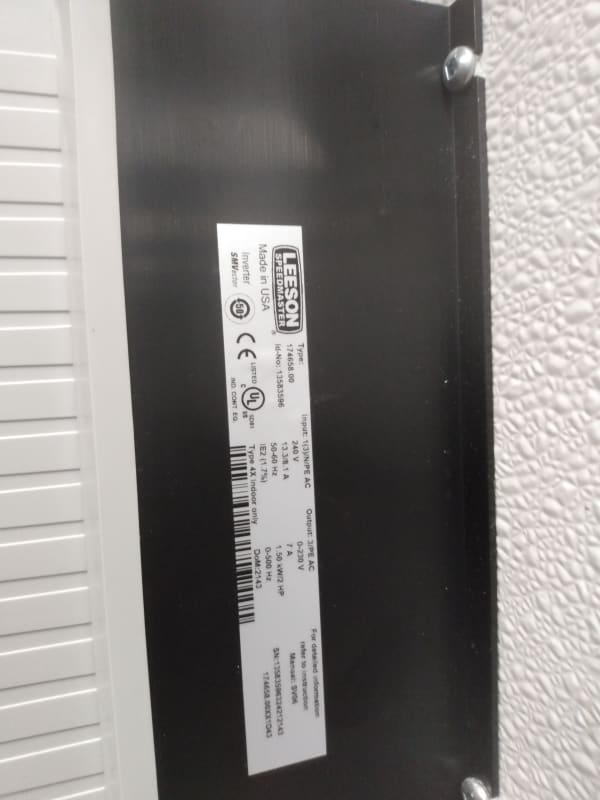
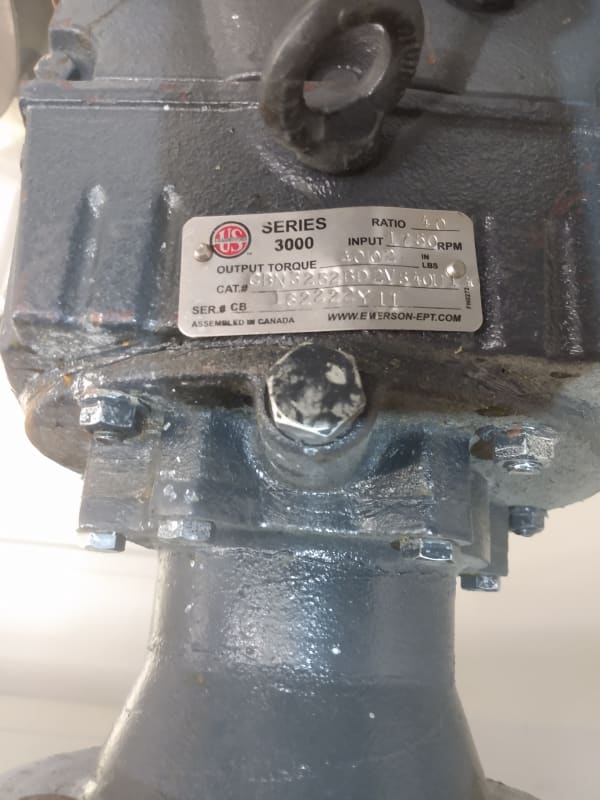