kingnero
Mechanical
- Aug 15, 2009
- 1,758
See attached pics, approx. 100 ft pole for overhead electrical lines with a circular baseplate mounted on threaded studs.
Doesn't look that old, however the installation has been in service for a few years, so unlikely that grouting is still planned to do.
There is no cable (apart from a ground strap) that goes from the pole to the concrete foundation (even though it looks like that).
What could be the reason grouting is not done?
Doesn't look that old, however the installation has been in service for a few years, so unlikely that grouting is still planned to do.
There is no cable (apart from a ground strap) that goes from the pole to the concrete foundation (even though it looks like that).
What could be the reason grouting is not done?
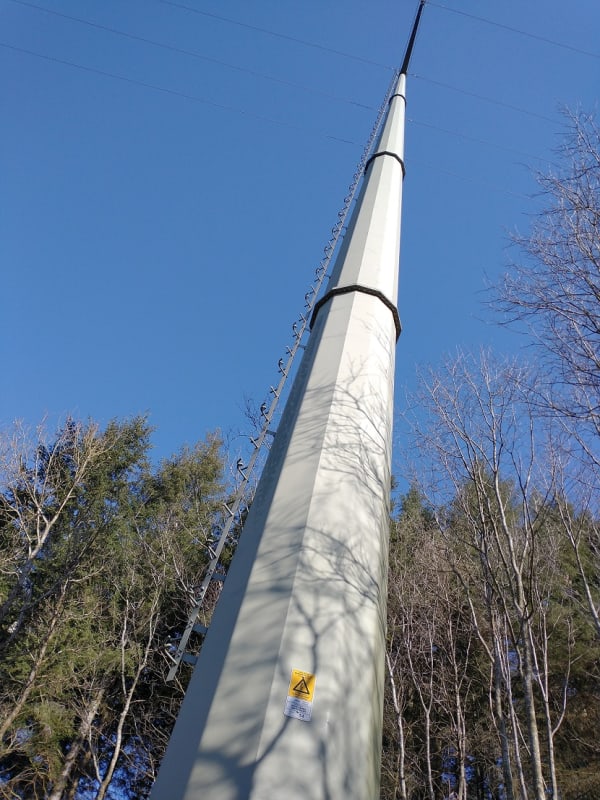
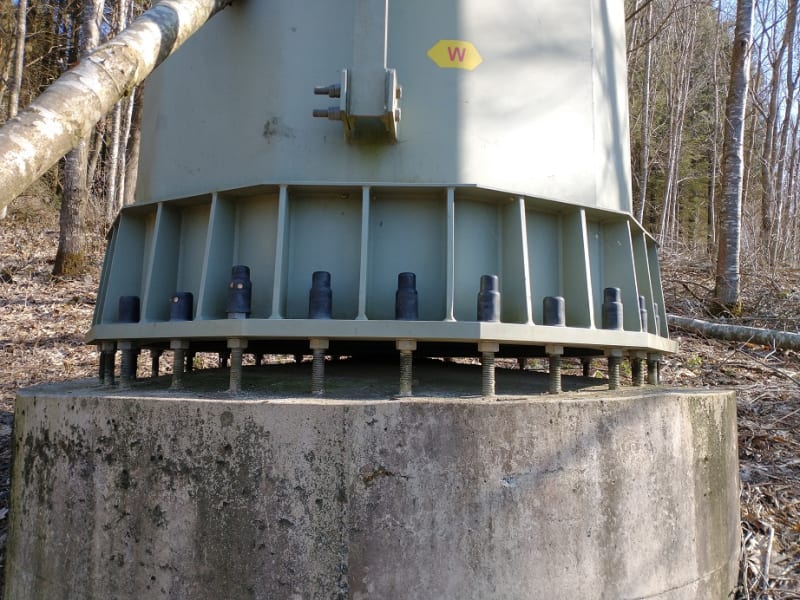