FacEngrPE
Mechanical
- Feb 9, 2020
- 1,643
I am going to offer a different theory of failure, based on some knowledge of slewing ring bearings, and this enlarged clip of the top of the mast, which looks like it is still circular. This indicates (to me) that the mast tube did not fail in buckling.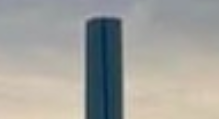
Slewing bearings have very exacting bolt tension requirements. They also have periodic re-tightening requirements. Low bolt tension can increase the risk of bolt fatigue failure.
Slewing rings have also been known to have internal failures which can lead to rapid disassembly.
By this theory the failure could have occurred at a time when the windspeed was much lower than the stated design speed,
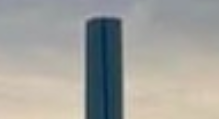
Slewing bearings have very exacting bolt tension requirements. They also have periodic re-tightening requirements. Low bolt tension can increase the risk of bolt fatigue failure.
Slewing rings have also been known to have internal failures which can lead to rapid disassembly.
By this theory the failure could have occurred at a time when the windspeed was much lower than the stated design speed,