Brad805
Structural
- Oct 26, 2010
- 1,518
I have been asked by a client to design a truck/car wash using wood trusses over the bays. I am not a fan of this at all, and I sketched out a precast alternate. The precast roof leads to more steps to create the roof finish they desire, and they are adamant about using wood trusses. The owner of the property has another car wash that used wood trusses, so they are not receptive to our concerns. At this point, I have not committed to complete the project, but I indicated we would investigate the solution briefly before stepping away from the project.
The general arch section is not any different than any typical residential application at this point. I have sketched the basics below.
Below is Technical bulletin from the Truss Plate Industry of Canada that discusses the use of wood trusses in a corrosive environment.
TPIC Bulletin
Wet v. dry moisture.
Currently they have not retained a mechanical engineer since that is not required due to the building size. I am not sure the air handling system will be stellar. I am trying to persuade them to add a mech eng since having a plan will be very helpful for the precast concrete aspects.
Questions:
1. Would you consider the attic space a moist environment and use the additional steps to protect the wood trusses? If so, I can probably just walk away at this point and save myself the headache.
2. Any experience with this? I found some discussions of others doing this, and a few plan submissions where they were doing so. The plans I found did not indicate anything special.
The general arch section is not any different than any typical residential application at this point. I have sketched the basics below.
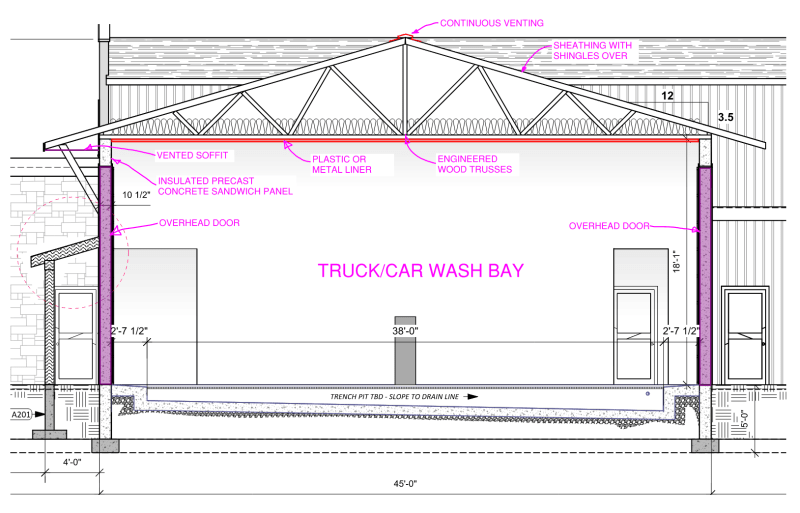
Below is Technical bulletin from the Truss Plate Industry of Canada that discusses the use of wood trusses in a corrosive environment.
TPIC Bulletin
Wet v. dry moisture.
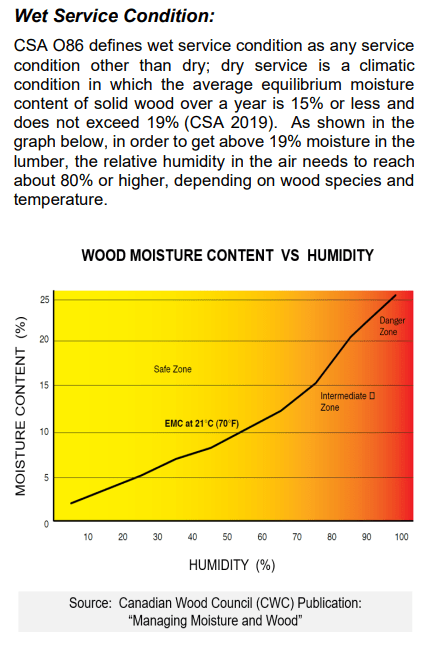
Currently they have not retained a mechanical engineer since that is not required due to the building size. I am not sure the air handling system will be stellar. I am trying to persuade them to add a mech eng since having a plan will be very helpful for the precast concrete aspects.
Questions:
1. Would you consider the attic space a moist environment and use the additional steps to protect the wood trusses? If so, I can probably just walk away at this point and save myself the headache.
2. Any experience with this? I found some discussions of others doing this, and a few plan submissions where they were doing so. The plans I found did not indicate anything special.