Hi,
I was looking at some wooden beams for redoing the floor online. I see this crack sort of thing in all the beams supporting the floor. what are those? That cannot be the crack in the beams due to beam overstress. I see that on all beams. Trying to understand what those are.
when I shop for new beams, I see that in the new beams as well. Is it to accommodate thermal expansion?
Thanks
I was looking at some wooden beams for redoing the floor online. I see this crack sort of thing in all the beams supporting the floor. what are those? That cannot be the crack in the beams due to beam overstress. I see that on all beams. Trying to understand what those are.
when I shop for new beams, I see that in the new beams as well. Is it to accommodate thermal expansion?
Thanks
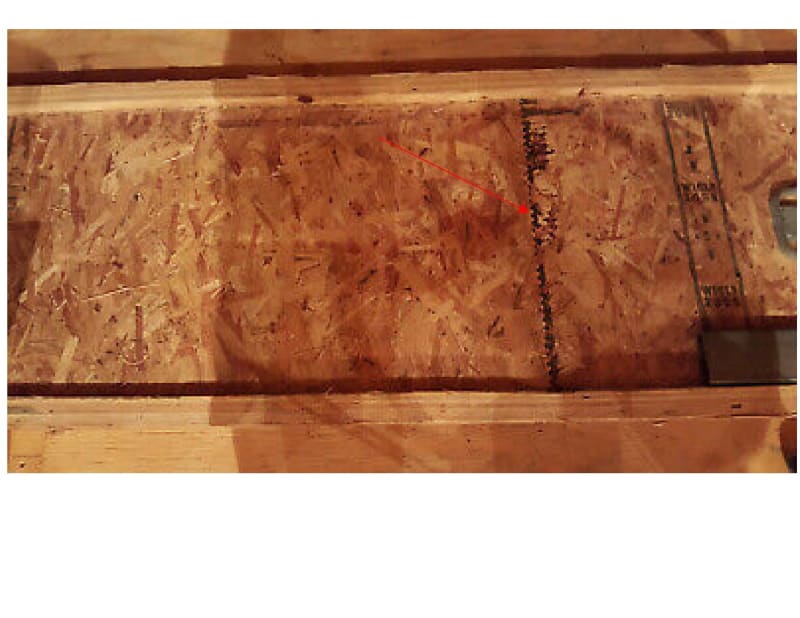