dejan95
Mechanical
- Aug 24, 2020
- 60
Hello everyone!
I have recently started my mechanical engineering (mechanical design) job. I was a handed a project of designing an assembly work station. I designed a tool which will hold my workpiece in place. The first picture bellow.
Because I was advised against using pneumatic cylinder for locking the workpiece in place (because we would like the station to be without pneumatics, only electricity), I'm searching for alternatives. I would like to use sensor which would activate the locking system (maybe electric cylinder) when the workpiece is places in the tool. The locking system would unlock once the worker would finish all operations on the part.
Do you maybe have any ideas what is the best way to lock part in place?
Picture bellow is without one part so you can see where the cylinder is supposed to fo:
I have recently started my mechanical engineering (mechanical design) job. I was a handed a project of designing an assembly work station. I designed a tool which will hold my workpiece in place. The first picture bellow.
Because I was advised against using pneumatic cylinder for locking the workpiece in place (because we would like the station to be without pneumatics, only electricity), I'm searching for alternatives. I would like to use sensor which would activate the locking system (maybe electric cylinder) when the workpiece is places in the tool. The locking system would unlock once the worker would finish all operations on the part.
Do you maybe have any ideas what is the best way to lock part in place?
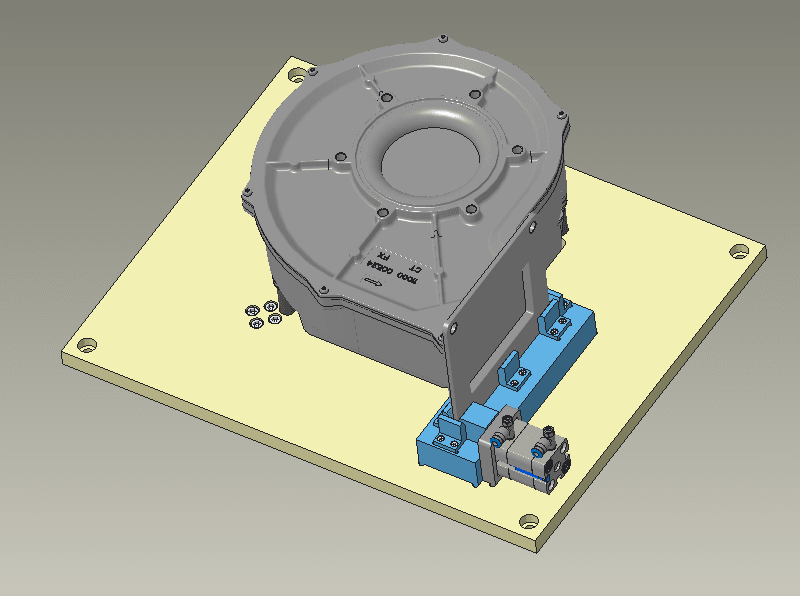
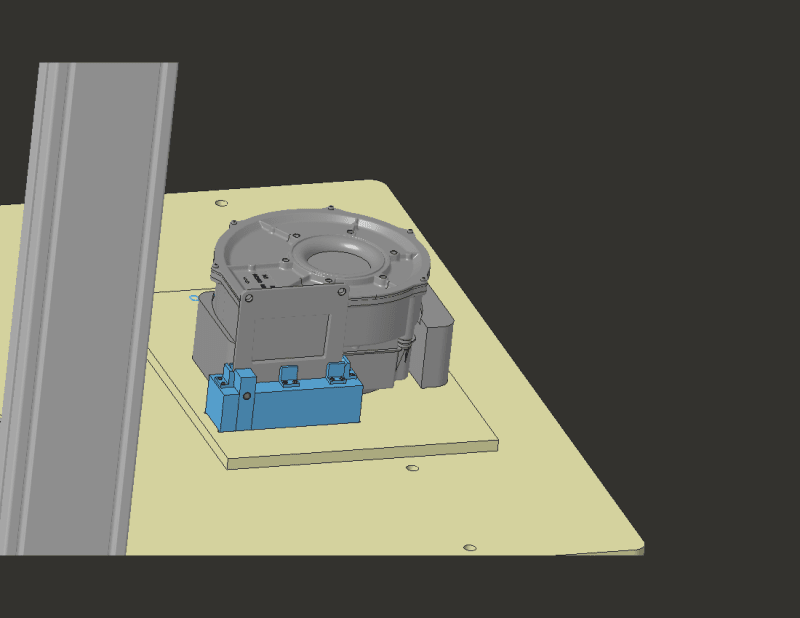
Picture bellow is without one part so you can see where the cylinder is supposed to fo:
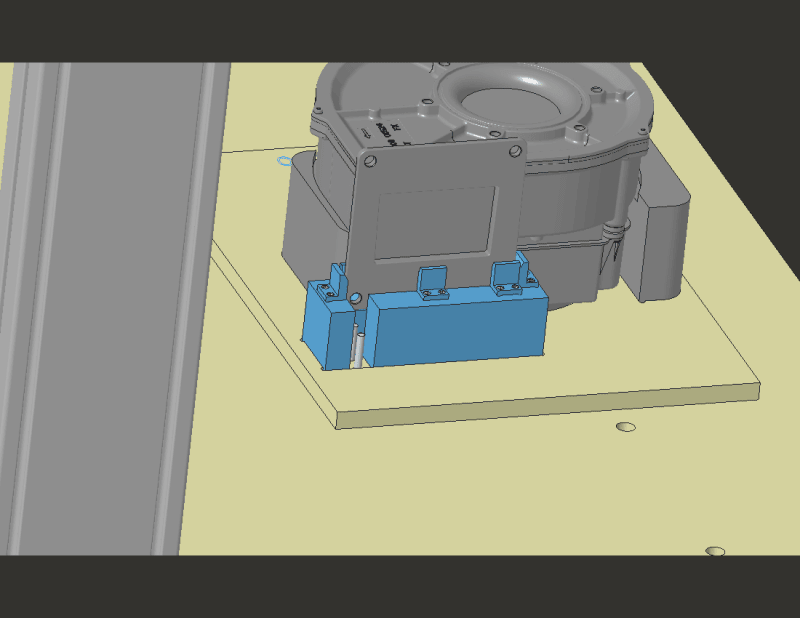