Folks, this question relates to ASME stress linearization when being done in ANSYS Mechanical. If I open ASME Sec. VIII, 5-A.4.1.2 and look at Step 2a, it states the bending stresses are only to be included for hoop and normal component stresses.
In Mechanical’s post-processing, there is an option to “zero through-thickness bending stress” when linearizing.
According to Help documentation, if set to Yes, it will exclude SX, SXY, and SXZ bending components (i.e., they will be set to zero). When set to YES, is that option in Mechanical intended to satisfy the ASME requirements?
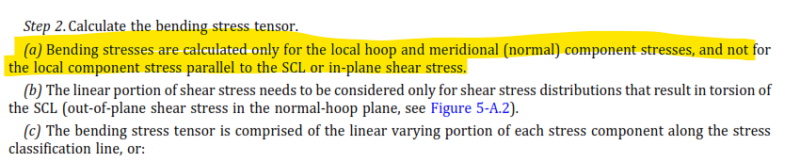
In Mechanical’s post-processing, there is an option to “zero through-thickness bending stress” when linearizing.
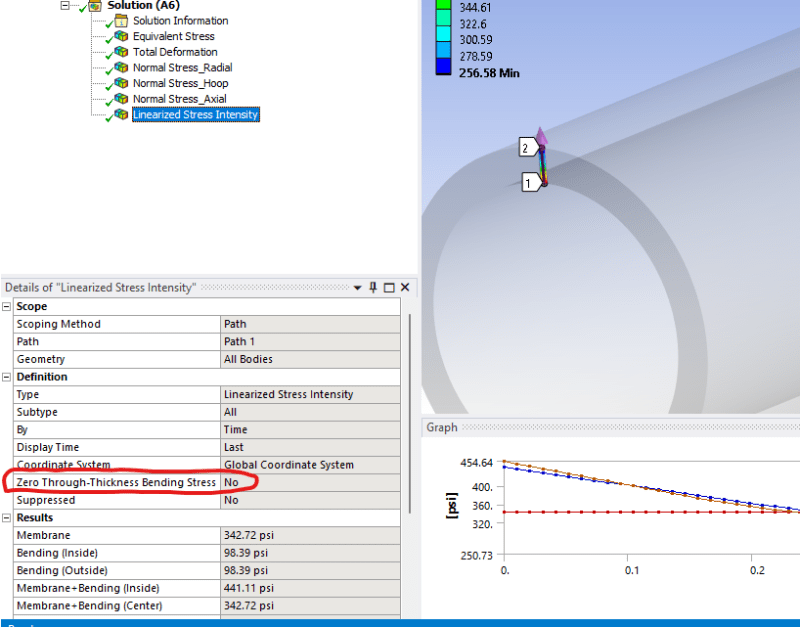
According to Help documentation, if set to Yes, it will exclude SX, SXY, and SXZ bending components (i.e., they will be set to zero). When set to YES, is that option in Mechanical intended to satisfy the ASME requirements?
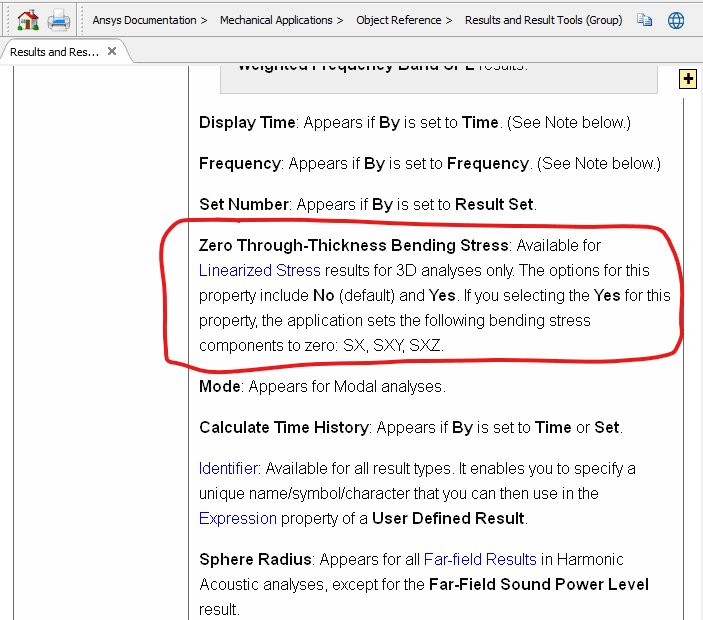