Good day;
This question has come up a few times in my world, and I'm hoping someone can point me in the right direction. I'm sure we've all seen pipe spools where someone has cheated while installing a slip on flange. The flange is "kicked" a bit to change the direction of a pipe. I've seen it done a lot, but I'm not sure if it is permissible by code. The spool I was shown today is probably one of the most extreme examples of a kicked flange that I've ever seen.
I've read a lot about the placement of the slip on flange in relation to the end of the pipe (set back for the weld). We do a lot of work in ASME B31.1 and B31.3, and these codes don't tell you the amount of setback to use (unlike AWWA where they are very specific about where to position the slip on flange in relation to the end of the pipe). I don't believe either ASME B31.1 or B31.3 address the kicking of a flange while welding it.
Material is 316L SS
Code is ASME B31.3
Flanges are B16.5 slip on (class 150)
The photos below show a spool that came in to our shop (not fabricated by us). It was field fabricated by one of our clients. The spool came back to repair an unrelated issue flagged by non-destructive testing of the welds. Our concern is that if we fix the issue and return to our client, the engineer will look at it and say the flange is not acceptable. I hear a lot of "we do it all time", but as we all know, that doesn't make it right. If this is a code issue, I'd like to notify our client right away so that we have the opportunity to fix it before it is returned to site. I know why they did it. It's a really ugly location, and they were looking for a quick fix to install a spool between two fixed points. I know we can provide a new spool to would have slip on square to the pipe, but I don't want to put that expense on our client if it isn't necessary.
Looking forward to hearing your thoughts on this. Thanks.
This question has come up a few times in my world, and I'm hoping someone can point me in the right direction. I'm sure we've all seen pipe spools where someone has cheated while installing a slip on flange. The flange is "kicked" a bit to change the direction of a pipe. I've seen it done a lot, but I'm not sure if it is permissible by code. The spool I was shown today is probably one of the most extreme examples of a kicked flange that I've ever seen.
I've read a lot about the placement of the slip on flange in relation to the end of the pipe (set back for the weld). We do a lot of work in ASME B31.1 and B31.3, and these codes don't tell you the amount of setback to use (unlike AWWA where they are very specific about where to position the slip on flange in relation to the end of the pipe). I don't believe either ASME B31.1 or B31.3 address the kicking of a flange while welding it.
Material is 316L SS
Code is ASME B31.3
Flanges are B16.5 slip on (class 150)
The photos below show a spool that came in to our shop (not fabricated by us). It was field fabricated by one of our clients. The spool came back to repair an unrelated issue flagged by non-destructive testing of the welds. Our concern is that if we fix the issue and return to our client, the engineer will look at it and say the flange is not acceptable. I hear a lot of "we do it all time", but as we all know, that doesn't make it right. If this is a code issue, I'd like to notify our client right away so that we have the opportunity to fix it before it is returned to site. I know why they did it. It's a really ugly location, and they were looking for a quick fix to install a spool between two fixed points. I know we can provide a new spool to would have slip on square to the pipe, but I don't want to put that expense on our client if it isn't necessary.
Looking forward to hearing your thoughts on this. Thanks.
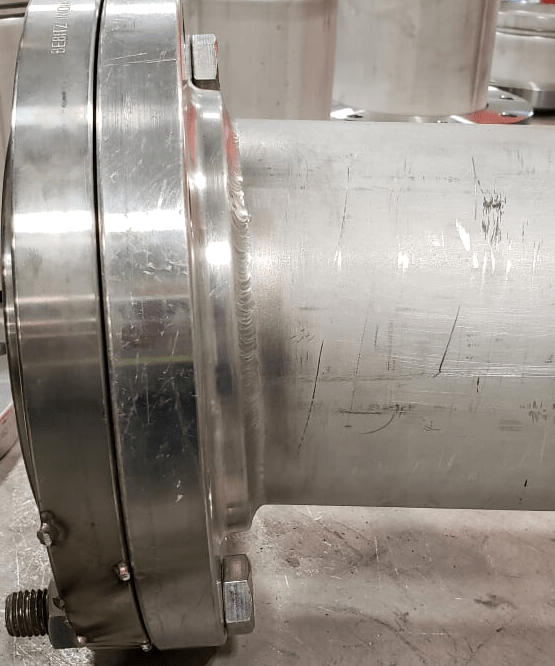
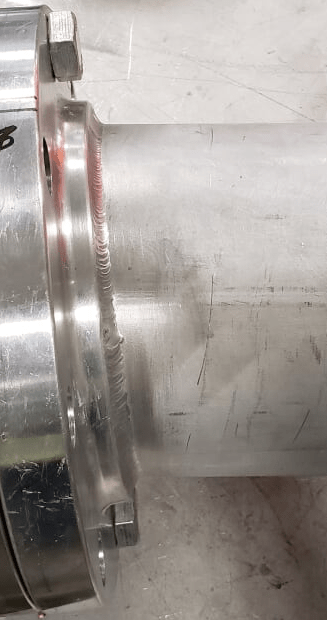
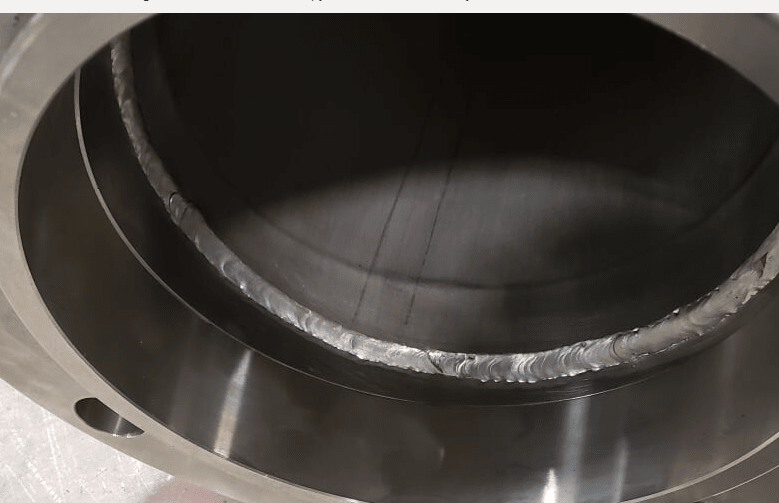