Tarator
Automotive
- Sep 20, 2013
- 176
Hi All,
Based on the measured values of the following external cylindrical feature of size on a rigid part, what would be the bonus tolerance for straightness?
Measured LMC = ø 8.006
Measured MMC = ø 11.527
Measured Actual Mating Size = ø 11.979
Measured straightness = ø 2.724
My answer is this:
1) Finding the size: Actual Mating Size - Straithness = 11.979 - 2.724 = 9.255
2) Bonus = MMC - Size = 12 - 9.255 = 2.745
Thank you.
Based on the measured values of the following external cylindrical feature of size on a rigid part, what would be the bonus tolerance for straightness?
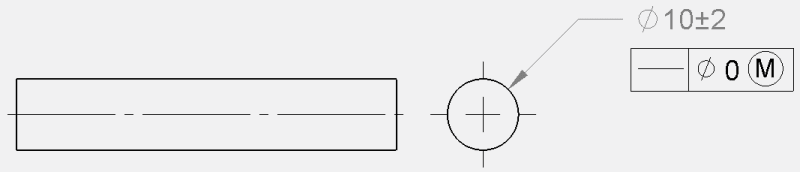
Measured LMC = ø 8.006
Measured MMC = ø 11.527
Measured Actual Mating Size = ø 11.979
Measured straightness = ø 2.724
My answer is this:
1) Finding the size: Actual Mating Size - Straithness = 11.979 - 2.724 = 9.255
2) Bonus = MMC - Size = 12 - 9.255 = 2.745
Thank you.