Hello!
Hopefully someone here can help me!
I am currently analyzing a glass DOUBLE IGU panel supported on both sides by structural silicone (please check pictures below).
I would like to know if there is any way to calculate the maximum stress on the silicone as a function of the weight and height of gluing the panel.
Currently, my spreadsheet is calculating the shear area of the silicone joint ( b x A) and divide it by half the height of the glass panel.
tau = (Weight/2)/(bxA) - Please note the pictures below
But I would like to know if there's any better way to design this silicone joints including any possible peel failure. I don't have much faith in this approach. I'm also afraid that some normal stress could arise due to bending in plane direction of the glass at mid span (although not significantly as the glass is pretty rigid). Does someone have any tips on how to properly design silicone joints?
Hopefully someone here can help me!
I am currently analyzing a glass DOUBLE IGU panel supported on both sides by structural silicone (please check pictures below).
I would like to know if there is any way to calculate the maximum stress on the silicone as a function of the weight and height of gluing the panel.
Currently, my spreadsheet is calculating the shear area of the silicone joint ( b x A) and divide it by half the height of the glass panel.
tau = (Weight/2)/(bxA) - Please note the pictures below
But I would like to know if there's any better way to design this silicone joints including any possible peel failure. I don't have much faith in this approach. I'm also afraid that some normal stress could arise due to bending in plane direction of the glass at mid span (although not significantly as the glass is pretty rigid). Does someone have any tips on how to properly design silicone joints?
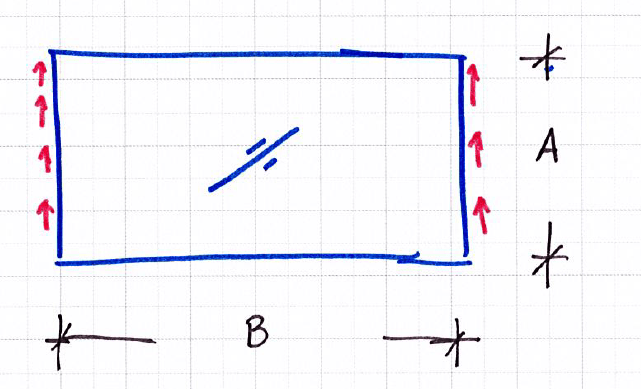
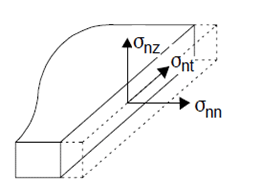
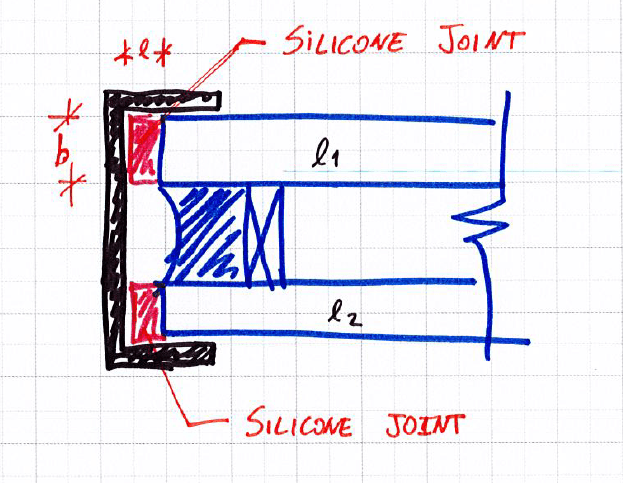
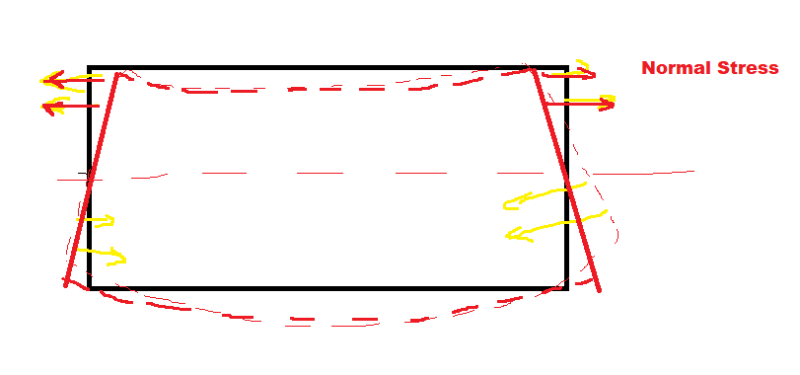