Jason3w
Mechanical
- Sep 26, 2016
- 3
Hi all.
We currently use a 3mm roll pin to secure an aluminium component inside a carbon fibre tube.
We drill a 3mm hole through the two parts and use a hammer with a decent force to insert the roll pin.
We have reports from customers of the roll pins working their way out of the two parts somehow.
The final product is a 1.5mt pole that is spinning when used and forces are applied to the centre of the pole with weights on the ends.
This is entirely baffling which is why I am here to see if anyone could explain why/how this could happen.
The two parts have very tight tolerance and we also use Araldite 2015 to glue in place prior to pinning.
Any ideas how this happens?
Images attached.
Thanks!
Pin worked out on parts and through the EPDM grip.
We currently use a 3mm roll pin to secure an aluminium component inside a carbon fibre tube.
We drill a 3mm hole through the two parts and use a hammer with a decent force to insert the roll pin.
We have reports from customers of the roll pins working their way out of the two parts somehow.
The final product is a 1.5mt pole that is spinning when used and forces are applied to the centre of the pole with weights on the ends.
This is entirely baffling which is why I am here to see if anyone could explain why/how this could happen.
The two parts have very tight tolerance and we also use Araldite 2015 to glue in place prior to pinning.
Any ideas how this happens?
Images attached.
Thanks!
Pin worked out on parts and through the EPDM grip.
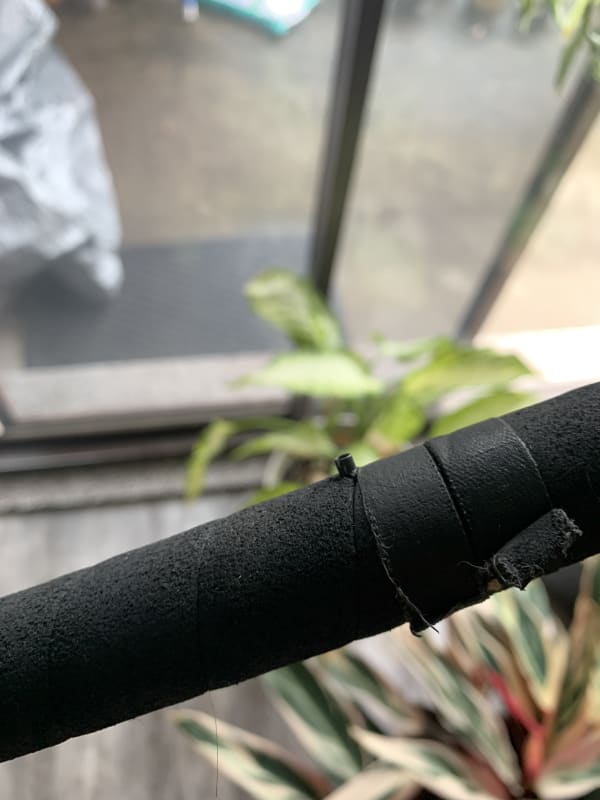
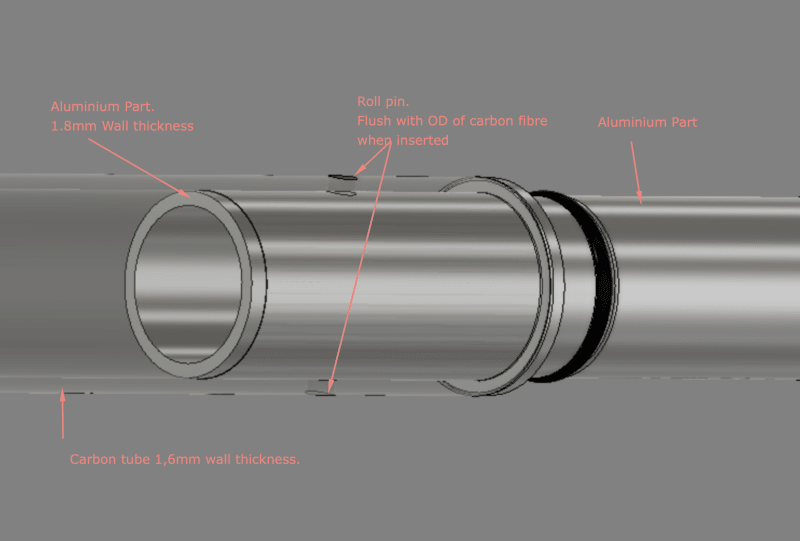