itsmoked
Electrical
- Feb 18, 2005
- 19,114
I have a cooling system as seen below that runs water/ethylene glycol mix to cool 13 zones via solenoids.
The pump charges a manifold that the zones draw from. Since temp controllers run the valves none can be open or most of them can be open. All of them are never open though perhaps half could be at once.
I want to spec a valve to bypass when needed to try and keep the supply pressure constant thru the loops while also avoiding dead-heading the pump. I have no idea what the correct term for this particular valve would be or where I should look for one. Given the details I've provided can I get some direction on what and where I should get one, preferably at the usual suspects.
Keith Cress
kcress -
The pump charges a manifold that the zones draw from. Since temp controllers run the valves none can be open or most of them can be open. All of them are never open though perhaps half could be at once.
I want to spec a valve to bypass when needed to try and keep the supply pressure constant thru the loops while also avoiding dead-heading the pump. I have no idea what the correct term for this particular valve would be or where I should look for one. Given the details I've provided can I get some direction on what and where I should get one, preferably at the usual suspects.
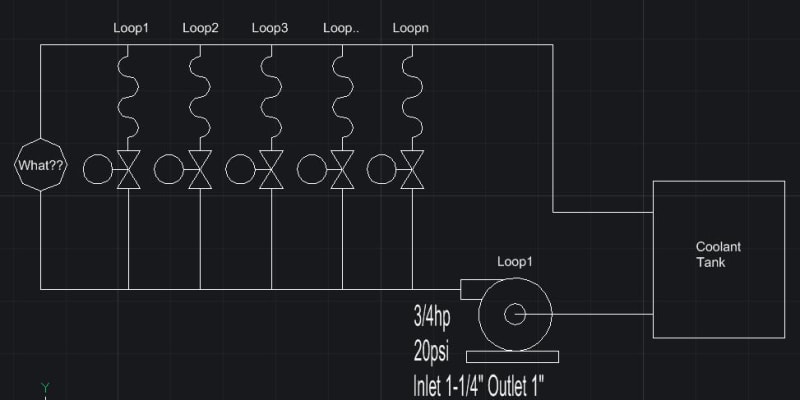
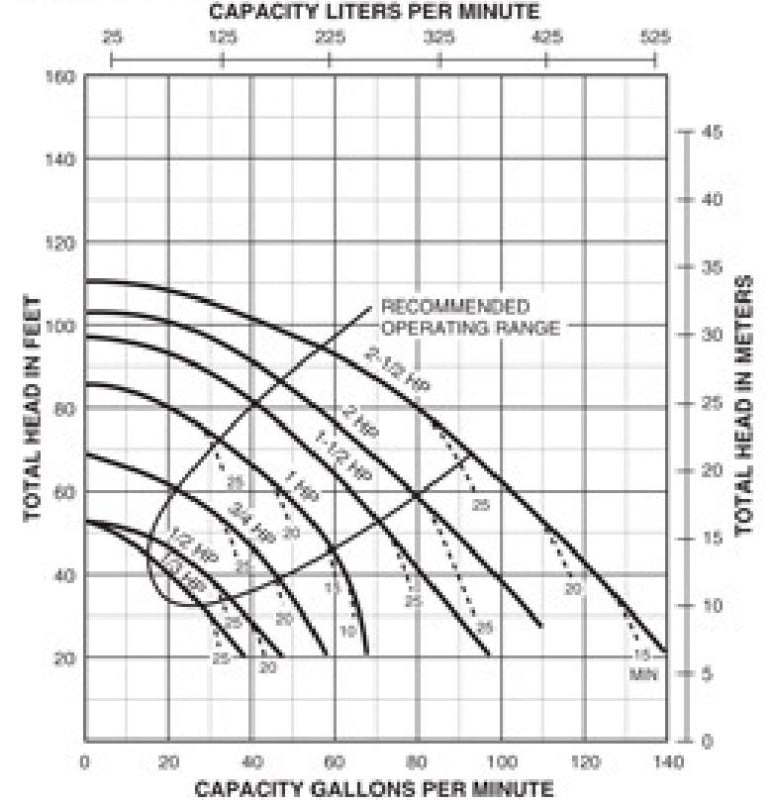
Keith Cress
kcress -