I am working on a building project where there are some piles that cannot be installed directly under the building columns. I am looking at a cantilever pile cap solution as sketched below. I have sketched the STM model over one of the stress diagrams. Is this STM model reasonable or could it be improved?
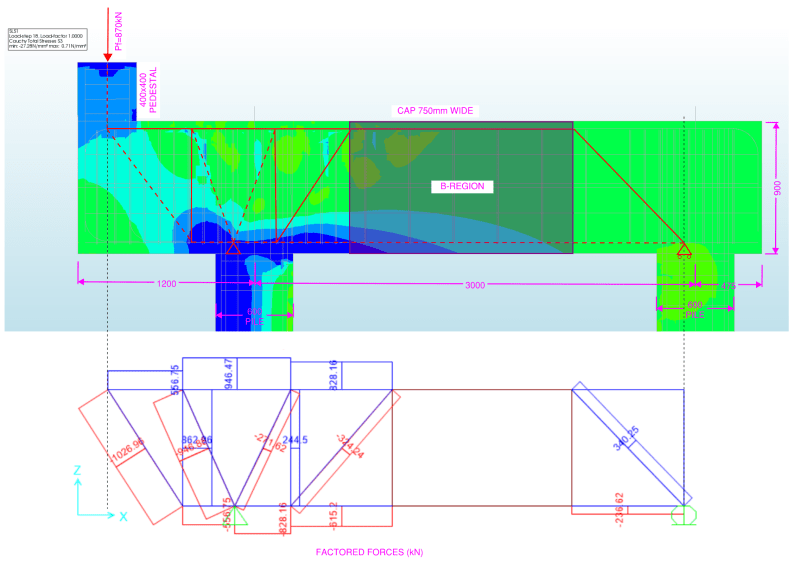