Imposter666
Mechanical
In the previous post, I had asked how to design the lift mechanism of this gantry []. Now I need your input how to move this mechanism 8 meters along the rails. For now, I have both sides resting on LM guides driven by a single motor on one side. There are objects between the LM guides so I can't connect the leg structures. In practice, it is extremely difficult to align the seats for the LM guides once installed on the ground. So I need to come up with a mechanism with more 'give'. I am thinking to switch to some kind of mechanism with rollers. What do you think of this idea? Do you have any suggestions?
Some input:
Rails are 2.5m apart.
Distance is 8m long.
This needs to be very sturdy mechanism with high cycle count.
Blue section is going to be close to 1000lb with the load it will carry.
Some input:
Rails are 2.5m apart.
Distance is 8m long.
This needs to be very sturdy mechanism with high cycle count.
Blue section is going to be close to 1000lb with the load it will carry.
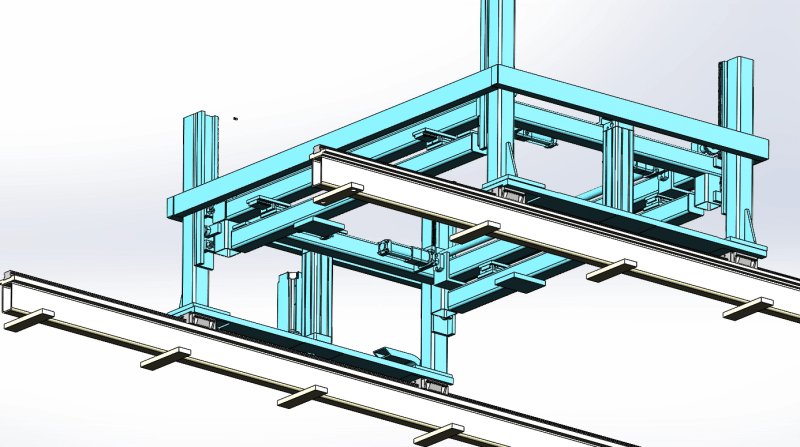
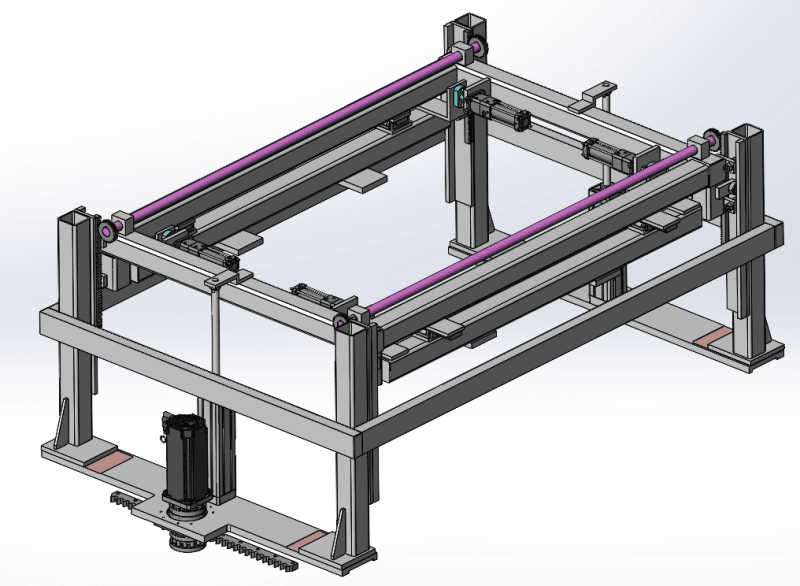
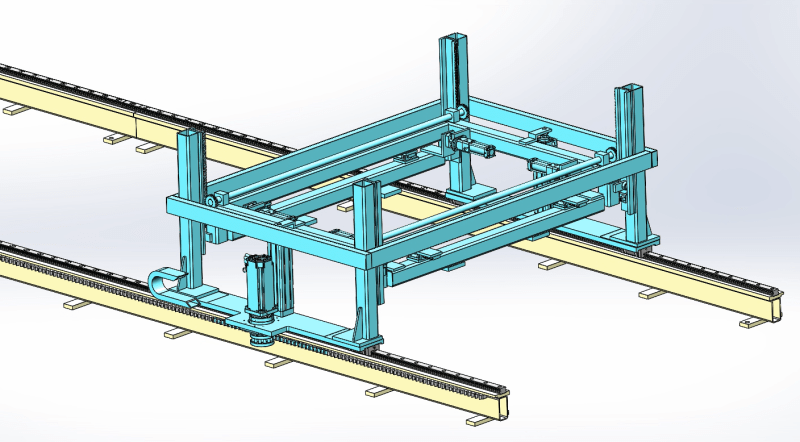
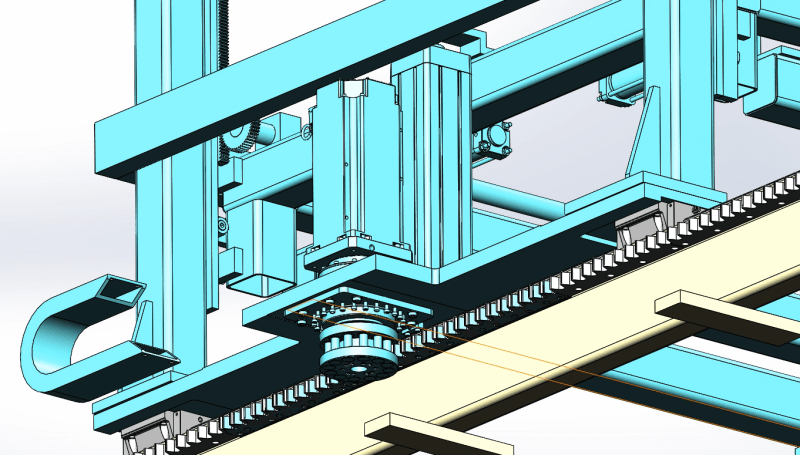