I am trying to come up with a fee proposal for a Waste Transfer Station. The job is basically a pre-engineered metal building foundation. But I noticed that they have what is called a "push wall". I did some research and I understand what it is.
Looking at the preliminary layout drawings, it almost seems that the PEMB columns must bear on top of the concrete push wall. Is this normal? From my research it seems that the PEMB columns are usually outboard of the push wall, and the foundations for each are separate entities. Are they ever constructed with the columns bearing on top of the wall?
Below is a picture that I found online. ANd below that is a screen shot of the preliminary drawing elevation. I will ask the architect for clarity - but I wanted to run it by you all to make sure this isn't a "stupid question".
Looking at the preliminary layout drawings, it almost seems that the PEMB columns must bear on top of the concrete push wall. Is this normal? From my research it seems that the PEMB columns are usually outboard of the push wall, and the foundations for each are separate entities. Are they ever constructed with the columns bearing on top of the wall?
Below is a picture that I found online. ANd below that is a screen shot of the preliminary drawing elevation. I will ask the architect for clarity - but I wanted to run it by you all to make sure this isn't a "stupid question".
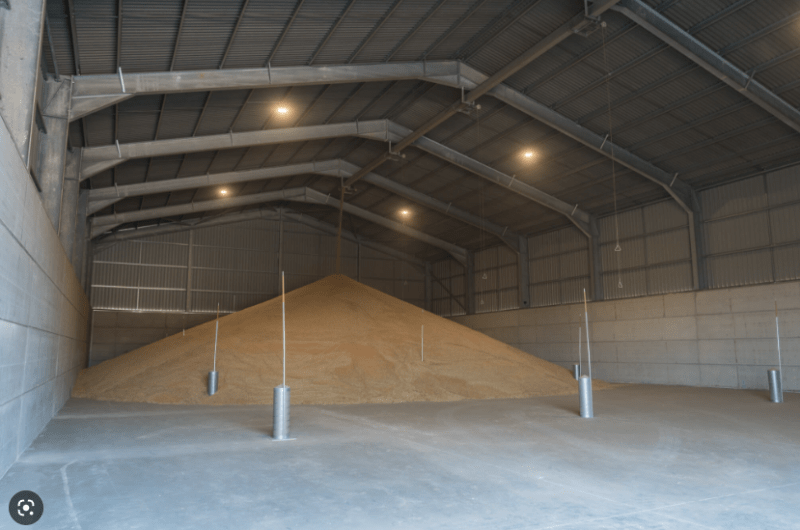
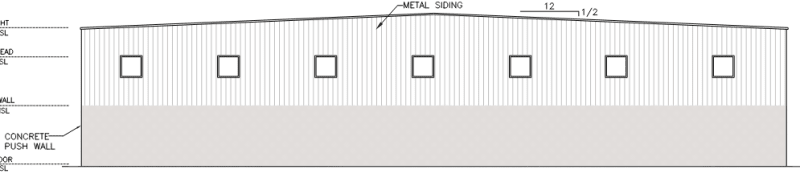