-
1
- #1
dik
Structural
- Apr 13, 2001
- 25,736
On a recent project, I require plates clamped to an HSS column with friction providing the vertical capacity. They don't want to drill or weld on site. I've attached a sketch of the connection. Any suggestions about maintaining the clamping force (my preference is Loctite Red) and determining the coeficient of friction? The material is HDG steel and the bolts are A325s. It is exposed to the elements and will probably cycle from -40C to +60C. One solution I haven't broached with the client is to use powder actuated fasteners with thinner clamping plates. I don't know if that is acceptable. I can easily calculate the crushing load of the HSS column walls.
-----*****-----
So strange to see the singularity approaching while the entire planet is rapidly turning into a hellscape. -John Coates
-Dik
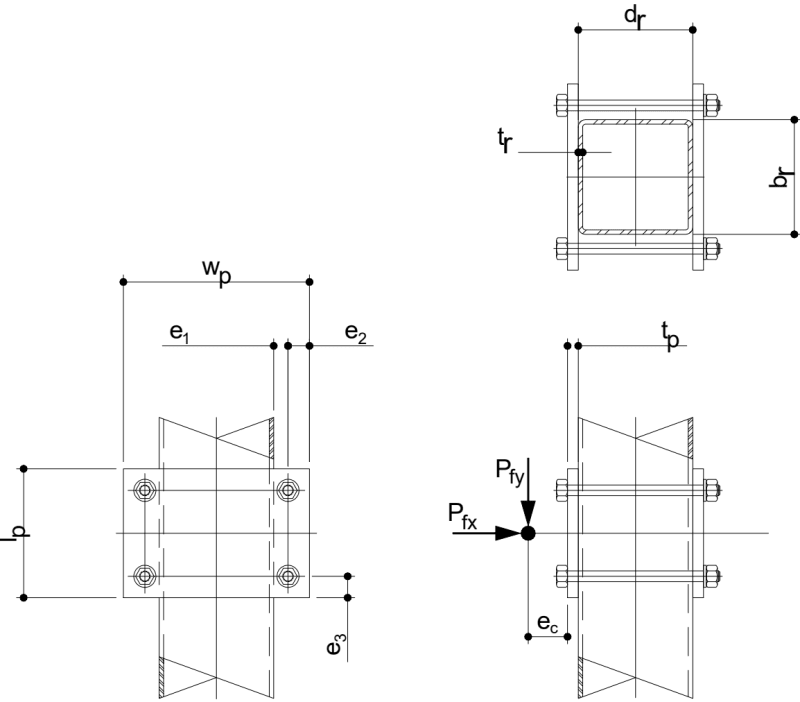
-----*****-----
So strange to see the singularity approaching while the entire planet is rapidly turning into a hellscape. -John Coates
-Dik