SatoshiNakamoto09
Structural
- Sep 2, 2014
- 25
Hello, let me know if I am posting in the right thread topic.
Should I confidently say that my structural model is correct? since I am getting the exact Tension cable by manual computation and structural analysis model result
Should I confidently say that my structural model is correct? since I am getting the exact Tension cable by manual computation and structural analysis model result
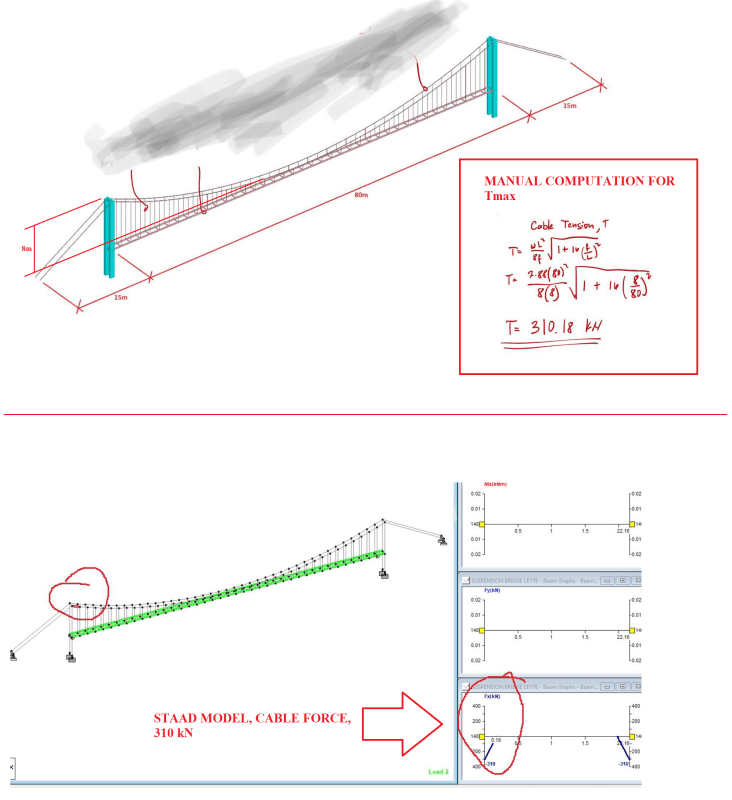