-
1
- #1
Context
- Grade beam on a local infrastructure project. It supports a fence that keeps sabre toothed tigers from eating babies. Low importance factor as with most livestock stuff.
- An unfortunate core has been made through the grade beam top reinforcing.
- Various constraints are making it desirable to get this repair done in as localized a manner a possible. The fence is already in place and its anchorages are nearby to the location where this repair will take place. The repair location is also very close to a plan "corner" where the grade beam changes direction over the pile.
- Quality control on this project is good. You know, other than this ridiculous core.
- One repair option being considered is field welded splices of the reinforcement. This is not weldable rebar, however, so we'd have to deal with preheat.
Questions
How good -- or bad -- of an idea is it to consider field welded reinforcement splices here from a QC perspective?
Is there any danger that the preheated bars would expand and cause the cover concrete of the grade beam to spall?
- Grade beam on a local infrastructure project. It supports a fence that keeps sabre toothed tigers from eating babies. Low importance factor as with most livestock stuff.
- An unfortunate core has been made through the grade beam top reinforcing.
- Various constraints are making it desirable to get this repair done in as localized a manner a possible. The fence is already in place and its anchorages are nearby to the location where this repair will take place. The repair location is also very close to a plan "corner" where the grade beam changes direction over the pile.
- Quality control on this project is good. You know, other than this ridiculous core.
- One repair option being considered is field welded splices of the reinforcement. This is not weldable rebar, however, so we'd have to deal with preheat.
Questions
How good -- or bad -- of an idea is it to consider field welded reinforcement splices here from a QC perspective?
Is there any danger that the preheated bars would expand and cause the cover concrete of the grade beam to spall?
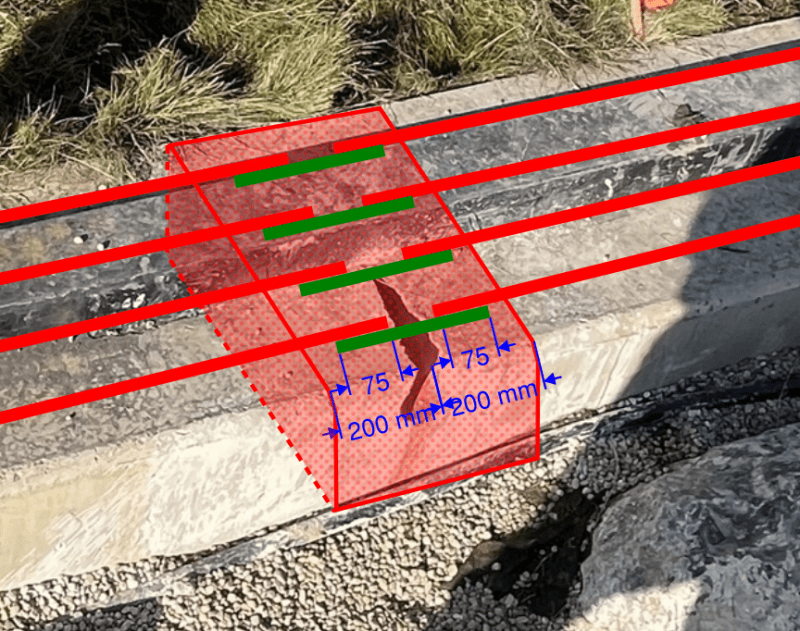
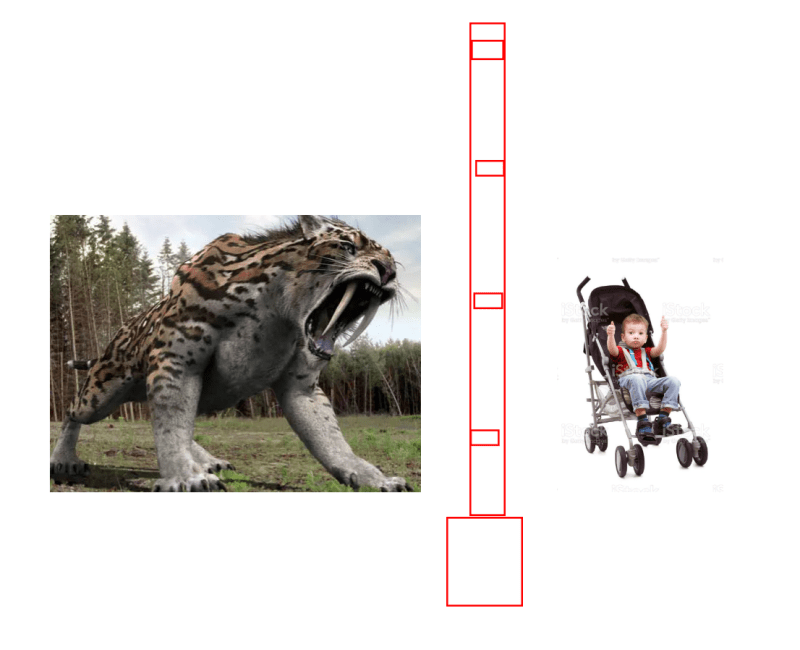