KrisWain320a
Automotive
Hi All,
I have been given a model with the following GD&T frame on one of the surfaces.
I am a little confused on the meaning/strategy of how to measure such a request. I work as a Metrology Engineer and trying to figure out how to measure such a request. From my understanding it is a composite surface profile tolerance meaning that surface has a profile tolerance of ±0.8 mm in respect to the |A|B(max)|C(max)| alignment system.
It's the second part that confused me. I assume it is asking for a ±0.2 mm tolerance over a 400 mm area? Does this mean breaking the surface up into smaller 400 mm^2 patches and no patch can be ±0.2 mm to itself. Or does it mean a point spacing of 400 mm.
For information the patch in question has an area of 48384 mm^2.
I am trying to understand exactly what the second tolerance is asking for and more importantly how I would set up the measures using an optical system? I have mesh data that I can apply all forms of inspection to but not sure how or what to set up to correctly represent this tolerance.
Any help would be greatly appreciated. The bottom tolerance is really confusing me.
I have been given a model with the following GD&T frame on one of the surfaces.
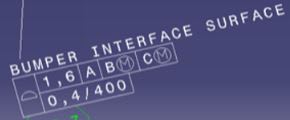
I am a little confused on the meaning/strategy of how to measure such a request. I work as a Metrology Engineer and trying to figure out how to measure such a request. From my understanding it is a composite surface profile tolerance meaning that surface has a profile tolerance of ±0.8 mm in respect to the |A|B(max)|C(max)| alignment system.
It's the second part that confused me. I assume it is asking for a ±0.2 mm tolerance over a 400 mm area? Does this mean breaking the surface up into smaller 400 mm^2 patches and no patch can be ±0.2 mm to itself. Or does it mean a point spacing of 400 mm.
For information the patch in question has an area of 48384 mm^2.
I am trying to understand exactly what the second tolerance is asking for and more importantly how I would set up the measures using an optical system? I have mesh data that I can apply all forms of inspection to but not sure how or what to set up to correctly represent this tolerance.
Any help would be greatly appreciated. The bottom tolerance is really confusing me.