StrEng007
Structural
- Aug 22, 2014
- 510
What method does a truss designer use to determine the base cut at the heel of a truss?
I know the equation used to determine the overall heel height; I'm not sure what rule the truss designer applies for the base cut.
Two examples from truss shop drawings (2x4 top chords in both examples):
Truss Heel, 6 1/16" = 3.5" / (cos 18.43°) + Base Cut
Base cut = 2 3/8"
Truss Heel, 6 1/2" = 3.5" / (cos 26.56°) + Base Cut
Base cut = 2 9/16"
I know the equation used to determine the overall heel height; I'm not sure what rule the truss designer applies for the base cut.
Two examples from truss shop drawings (2x4 top chords in both examples):
Truss Heel, 6 1/16" = 3.5" / (cos 18.43°) + Base Cut
Base cut = 2 3/8"
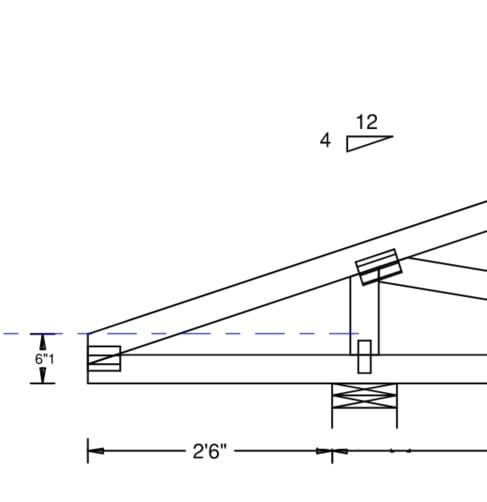
Truss Heel, 6 1/2" = 3.5" / (cos 26.56°) + Base Cut
Base cut = 2 9/16"
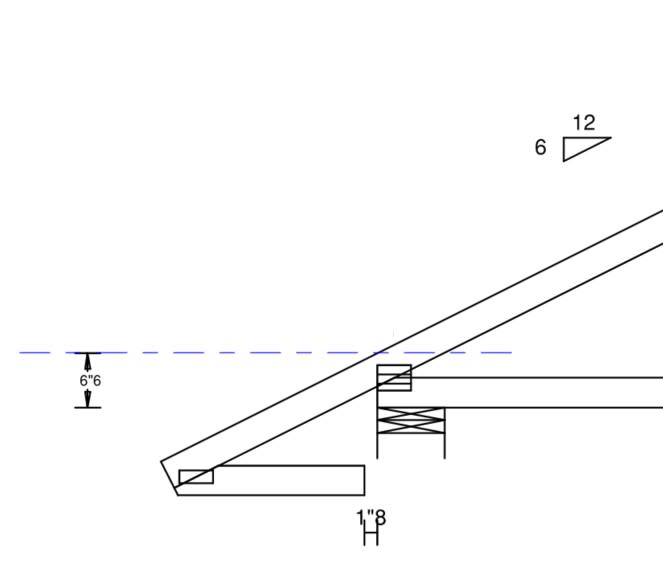