SeattleME
Mechanical
- Oct 9, 2023
- 12
Hi Everyone,
I’m a mechanical PE and could use some advice on the structural repair of a botch job an electrical contractor did at my house. I’ve attached some photos for reference.
I have about a dozen 2x10 floor joists over my garage. The kitchen is directly above the garage. The 2x10 joists have a span of approximately 17’-6”. An electrical contractor bored 2-inch diameter holes through the bottom section of the beams all the way across my garage. He installed a 100-amp subpanel on the other side for EV charging. The holes left about 1/2” of “meat” between the lower quadrant of the hole and the bottom surface of the beam. The holes are about eight feet from one end, positioned in the middle third of the beam. In effect, the electrician turned my 2x10s into 2x8s.
I’m in King County, Washington State, where the IRC is applicable. The IRC says no holes in the upper/bottom two inches of the joist. The inspector did his inspection via camera phone (didn’t even look at the joists) and passed it. I didn’t notice the issue until after the electrician left site (shame on me - wife says it’s my fault, but then again isn’t everything).
I will be proceeding with a repair for peace of mind, if nothing else. I don’t like the idea of reducing the load capacity of 2x10s that were already probably at max span. Especially not in my kitchen where people tend to congregate during social events. I’ve contacted the contractor but haven’t heard back yet. If he doesn’t agree to pay for the repair, he’ll be hearing from my attorney. I’m a forensic engineer, and as much as I don’t like to admit it, I know several dozen.
My questions (and thanks for reading this far) are:
1. Does anyone have any experience with joist reinforcement plates like those offered by Skyline Joist Repair ( While they look they’d work, the company has zero certifications and makes no code compliance claims whatsoever. However, if properly installed with screws and two-part epoxy, they look like they’d work okay as long as they more than make up for the deficit in the lost section modulus of the beam.
2. Would it be better to sister two 3/4” sheets of A-bond plywood on either side of the beam? Screwed and glued, of course.
3. Should I jack and level the beams before applying the repair in order to unload the beams near the stressed area? I don’t like the idea of encountering a flexural stress failure in the beam due to lack of composite action between the beam and the reinforcement plate or sisters.
Before someone suggests placing a Simpson strong-tie over it, I’ve read multiple opinions of SE’s saying that this won’t work due to the beam’s preload and lack of composite action between beam and tie; i.e., the beam will fail in flexure, then the load shifts to the tie, and then the tie fails — and all without any apparent increase in load carrying capability. Empirical evidence appears to support this position. There is a report from the 1970s where they tested metal straps running along the bottom of a joist. The straps were installed the full length of the joists. They found it didn’t help — the straps and wood failed independently of each other.
Appreciate the advice.
I’m a mechanical PE and could use some advice on the structural repair of a botch job an electrical contractor did at my house. I’ve attached some photos for reference.
I have about a dozen 2x10 floor joists over my garage. The kitchen is directly above the garage. The 2x10 joists have a span of approximately 17’-6”. An electrical contractor bored 2-inch diameter holes through the bottom section of the beams all the way across my garage. He installed a 100-amp subpanel on the other side for EV charging. The holes left about 1/2” of “meat” between the lower quadrant of the hole and the bottom surface of the beam. The holes are about eight feet from one end, positioned in the middle third of the beam. In effect, the electrician turned my 2x10s into 2x8s.
I’m in King County, Washington State, where the IRC is applicable. The IRC says no holes in the upper/bottom two inches of the joist. The inspector did his inspection via camera phone (didn’t even look at the joists) and passed it. I didn’t notice the issue until after the electrician left site (shame on me - wife says it’s my fault, but then again isn’t everything).
I will be proceeding with a repair for peace of mind, if nothing else. I don’t like the idea of reducing the load capacity of 2x10s that were already probably at max span. Especially not in my kitchen where people tend to congregate during social events. I’ve contacted the contractor but haven’t heard back yet. If he doesn’t agree to pay for the repair, he’ll be hearing from my attorney. I’m a forensic engineer, and as much as I don’t like to admit it, I know several dozen.
My questions (and thanks for reading this far) are:
1. Does anyone have any experience with joist reinforcement plates like those offered by Skyline Joist Repair ( While they look they’d work, the company has zero certifications and makes no code compliance claims whatsoever. However, if properly installed with screws and two-part epoxy, they look like they’d work okay as long as they more than make up for the deficit in the lost section modulus of the beam.
2. Would it be better to sister two 3/4” sheets of A-bond plywood on either side of the beam? Screwed and glued, of course.
3. Should I jack and level the beams before applying the repair in order to unload the beams near the stressed area? I don’t like the idea of encountering a flexural stress failure in the beam due to lack of composite action between the beam and the reinforcement plate or sisters.
Before someone suggests placing a Simpson strong-tie over it, I’ve read multiple opinions of SE’s saying that this won’t work due to the beam’s preload and lack of composite action between beam and tie; i.e., the beam will fail in flexure, then the load shifts to the tie, and then the tie fails — and all without any apparent increase in load carrying capability. Empirical evidence appears to support this position. There is a report from the 1970s where they tested metal straps running along the bottom of a joist. The straps were installed the full length of the joists. They found it didn’t help — the straps and wood failed independently of each other.
Appreciate the advice.
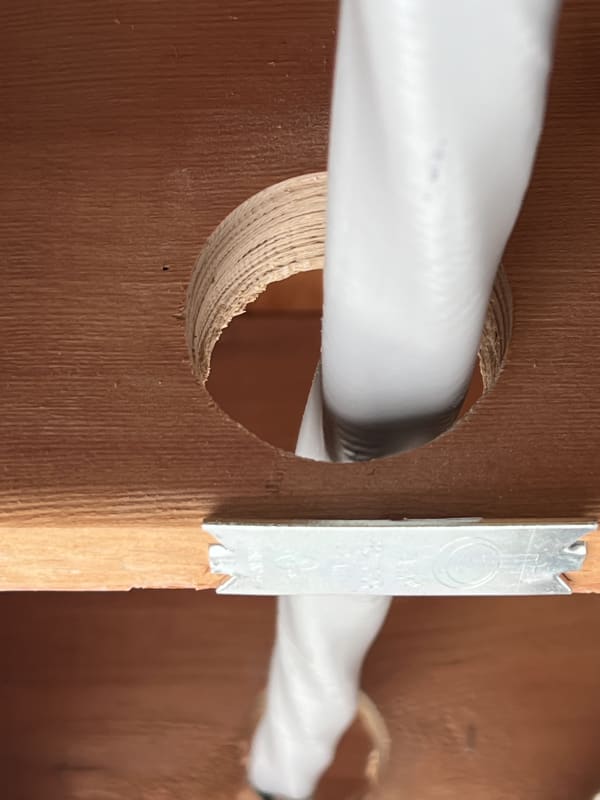
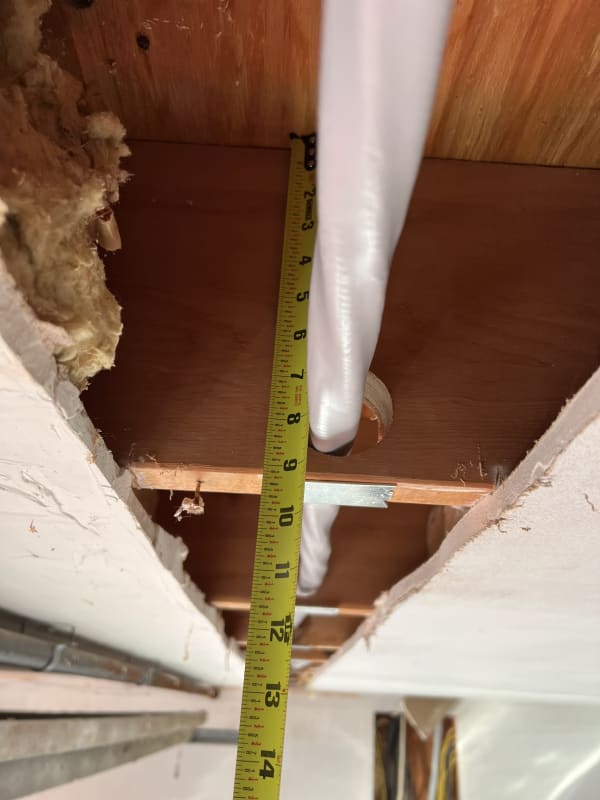
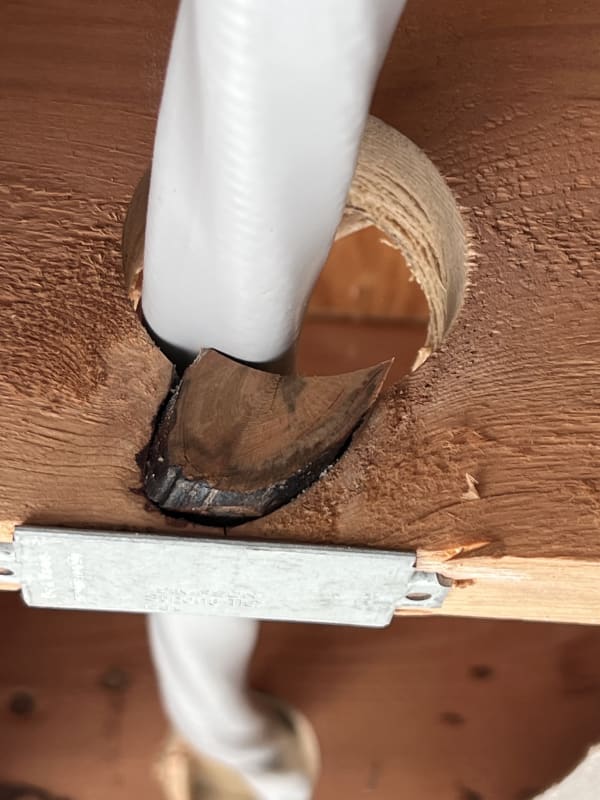