Hello everyone,
I'm currently working on a piping system of a live steam pipeline (around 500 m long) which serves as a main feed for turbine: DN200, s = 12.5 mm; T = 450°C; p = 68 bar(g).
I am doing a static analysis with ROHR2 software.
I have done numerous analysis for chemical facilities, but mostly on a much smaller scale.
My goal is to design the system with the appropriate number of expansion loops without unnecessarily overdoing it.
I am limited by pipe stress, support loads, thermal displacements and the possibility of fluid hammer, which increases the anchor loads proportionally to the length of the straight pipe section.
1) What would be a reasonable displacement/movement limit for a pipe shoe due to thermal expansion?
Is it limited by support design only and available space on the site?
Are there values from experience or technical literature that I can refer to?
Example: sketch below shows the position of the pipe shoe with 180 mm displacement (from -90 mm to +90 mm position) on a beam.
From my point of view it would be more economical to adjust the sliding surface to accommodate the movement than to make a loop.
2) Are there any case studies or examples of successful designs for similar piping systems that I can learn from?
3) In your opinion could a standard fix point - clamped, not welded (not an anchor), serve as a rotating point for a Z-expansion loop according to image below?
I'm interested in understanding best practices in minimizing unnecessary expansion loops and having reasonable pipe support loads.
I appreciate any insights, experiences, or references you can share. Thank you in advance!
Best regards,
Tomislav
I'm currently working on a piping system of a live steam pipeline (around 500 m long) which serves as a main feed for turbine: DN200, s = 12.5 mm; T = 450°C; p = 68 bar(g).
I am doing a static analysis with ROHR2 software.
I have done numerous analysis for chemical facilities, but mostly on a much smaller scale.
My goal is to design the system with the appropriate number of expansion loops without unnecessarily overdoing it.
I am limited by pipe stress, support loads, thermal displacements and the possibility of fluid hammer, which increases the anchor loads proportionally to the length of the straight pipe section.
1) What would be a reasonable displacement/movement limit for a pipe shoe due to thermal expansion?
Is it limited by support design only and available space on the site?
Are there values from experience or technical literature that I can refer to?
Example: sketch below shows the position of the pipe shoe with 180 mm displacement (from -90 mm to +90 mm position) on a beam.
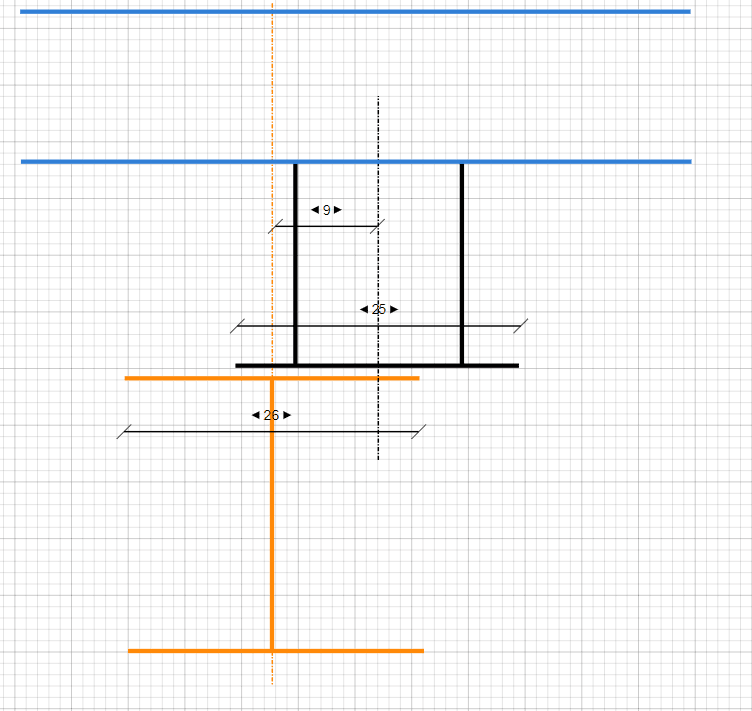
From my point of view it would be more economical to adjust the sliding surface to accommodate the movement than to make a loop.
2) Are there any case studies or examples of successful designs for similar piping systems that I can learn from?
3) In your opinion could a standard fix point - clamped, not welded (not an anchor), serve as a rotating point for a Z-expansion loop according to image below?
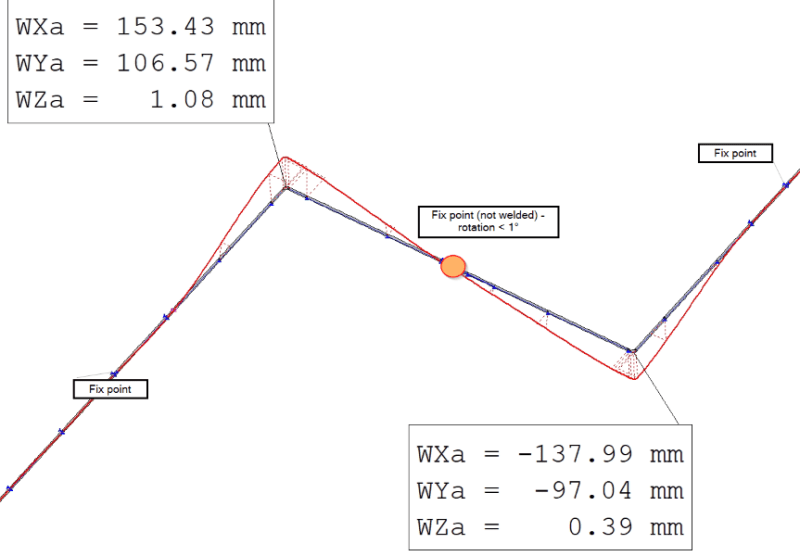
I'm interested in understanding best practices in minimizing unnecessary expansion loops and having reasonable pipe support loads.
I appreciate any insights, experiences, or references you can share. Thank you in advance!
Best regards,
Tomislav