Hi there,
I'm new to this forum. I am a DIY mechanic who also has an interest in metalworking. I hope my topic is interesting enough for this forum. As it is primary used for professionals sharing knowledge on work projects.
Alright this is the rear axle beam on my 905 kg, FWD car. A 1997 Toyota Starlet.
The rear axle is equipped with a panhard rod. I purchased a performance panhard rod but I found out that the bushing on the panhard is wider than the original from Toyota.
This is the mounting point on the rear axle for the panhard. The shoulder needs to be 6mm longer for the wider bushing to fit on. The axle beam is a U shape with a wall thickness of 4mm. At the panhard mounting point the U shape is reinforced with another U shape over it.
The panhard mounting shaft does penetrate through the axle beam and is welded on both ends. I think the section that goes through the axle beam is about 8mm thick. The picture below shows how the rear end of this shaft is welded on the axle beam.
My objective is to grind away this shaft and redesign the shaft with the correct dimensions. But how to make this strong enough to be used on a car? As suspension parts are usually mounted with class 10.9 fasteners, that strength is something to aim for. So at least a yield strength of 1040 N/mm2. Alloys such as 4140 and 4340 must be heat treated in order to reach such a strength. I also know that with welding I will reverse the strength of the heat treatment in that area. But to what kind of depth? Are there ways to mitigate the reduction of the strength during welding? Like selecting a specific alloy for this. I do have a TIG machine and ER80S-D2 filler rods. Would that seem fine for this?
Thank you very much for your attention and time.
I'm new to this forum. I am a DIY mechanic who also has an interest in metalworking. I hope my topic is interesting enough for this forum. As it is primary used for professionals sharing knowledge on work projects.
Alright this is the rear axle beam on my 905 kg, FWD car. A 1997 Toyota Starlet.
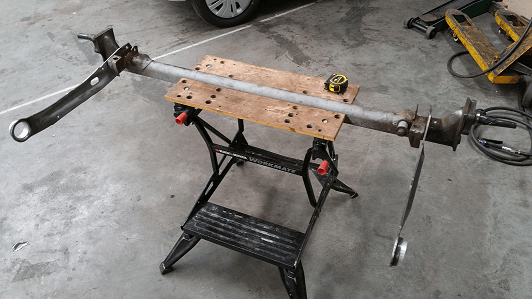
The rear axle is equipped with a panhard rod. I purchased a performance panhard rod but I found out that the bushing on the panhard is wider than the original from Toyota.
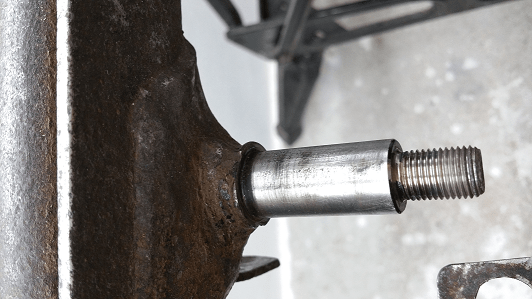
This is the mounting point on the rear axle for the panhard. The shoulder needs to be 6mm longer for the wider bushing to fit on. The axle beam is a U shape with a wall thickness of 4mm. At the panhard mounting point the U shape is reinforced with another U shape over it.
The panhard mounting shaft does penetrate through the axle beam and is welded on both ends. I think the section that goes through the axle beam is about 8mm thick. The picture below shows how the rear end of this shaft is welded on the axle beam.
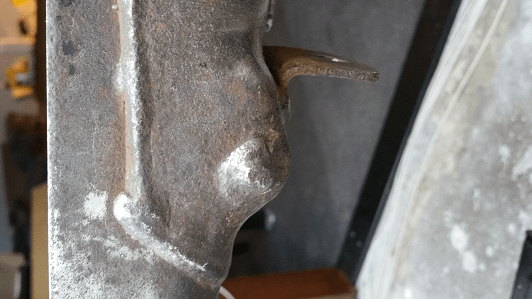
My objective is to grind away this shaft and redesign the shaft with the correct dimensions. But how to make this strong enough to be used on a car? As suspension parts are usually mounted with class 10.9 fasteners, that strength is something to aim for. So at least a yield strength of 1040 N/mm2. Alloys such as 4140 and 4340 must be heat treated in order to reach such a strength. I also know that with welding I will reverse the strength of the heat treatment in that area. But to what kind of depth? Are there ways to mitigate the reduction of the strength during welding? Like selecting a specific alloy for this. I do have a TIG machine and ER80S-D2 filler rods. Would that seem fine for this?
Thank you very much for your attention and time.