Michel60
Structural
- Aug 7, 2012
- 118
I've lurked around the site for a number of years now, offering my $0.02 occasionally (maybe two-bits with inflation and tariff). I now have a question for the group about a proposed truss profile for a residential project where my first reaction is a "hell no", see below. Its 45' long with a maximum depth slightly over 3'-4". To be fair to the truss designer they were asked by the client (without consulting me first, I was assuming that the area would be stick framed) to generate a budget so this is still a fictitious design right now to get to a preliminary cost. The "special trusses" are for a low-slope (<1:12) membrane roof, but the "girder trusses" support about an additional 12' tributary of a 3.5:12 slate roof.
So far I've only seen the profile summary, no calcs. But even with calcs saying it works I'm not inclined to accept the results. I can't imagine that typical truss design software can really handle this problem reliably. I know some of the regulars here have a pretty strong background in plate truss design so my questions to them are:
1) Do you see this as a legitimate truss profile (either typical or girder)?
2) If you do, can the common truss programs out there adequately design something like this?
Thanks!
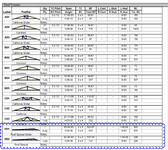
So far I've only seen the profile summary, no calcs. But even with calcs saying it works I'm not inclined to accept the results. I can't imagine that typical truss design software can really handle this problem reliably. I know some of the regulars here have a pretty strong background in plate truss design so my questions to them are:
1) Do you see this as a legitimate truss profile (either typical or girder)?
2) If you do, can the common truss programs out there adequately design something like this?
Thanks!
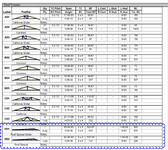