Josh Danziger
Marine/Ocean
Hi,
Confession first: I am not an engineering professional----so I realise that my question may get moderated away before it even sees the light of day! But if so I'm not sure where to take it ......
I am the owner of the 1911 Bristol Channel pilot cuter Cornubia. Now sailing Victorian or Edwardian workboats without winches, just with block-and-tackle, is knackering, and I decided that rather than have everyone pre-knackered before they even start sailing by raising the anchor on a manual windlass I would buy an electric one. Lofrans Falkon seemed to look reasonably timeless, and is a suitable size for 31tonne vessel, and we are just installing it now. What rather took me aback was that it is fixed with 4no ~11mm mounting holes (I think 7/16"), with plastic liners taking the size down to 10mm. GIven that the weight is borne primarily by the aft mountings this means that two m10 bolts are doing most of the work ...
This just seemed wrong, and indeed a quick check on some website gave the breaking load in shear of a4 m10 bolts (or maybe set screws) of around 0.8 tonne-force. (Obviously bolts have to be marine grade)
To put this in context, I've seen rule-of-thumb indications that anchor rode strength should be about 25% of boat weight, and this ties in with the ~7-8 tonne-force strength of our 12mm hot-dip galv chain; now it's very poor practice to leave the load on the windlass when anchored (you transfer it to a strong point on the boat), but 2no 0.8tonne-force still seemed very low.
POssibilities I considered were
1)Use some form of HT bolt: A4-80, 1.4462 duplex, 17-4ph, 8.8 hot-dip galv, 10.9 hot dip galv. I couldn't find 17-4ph or 10.9 hot-dip galv off the shelf; and 8.8 hot-dip galv didn't seem to have that much over a4-80 (both have tensile strength >800MPa) , so material choice came down to A4-80 or 1.4462 duplex.
2)Use 7/16 UNC or better still UNF bolts---but this would have meant removing the plastic liners (risking galvanic corrosion) and/or enlarging the holes (but the flanges didn't seem that huge to start with, and I worried about weakening the structure). Obviously I could have enlarged further (eg m12) but this was have magnified my concerns further ... so I decided to stick with m10.
So the eventual decision was to use M10 bolts (not set screws) in a4-80 or 1.4462; but web research showed that 1.4462 has strength ~650-850MPa, and a4-80 is advertised as 800 MPa+. So my first question is what justifies the huge expense (comparatively) of 1.4462 if it's weaker than a4-80 (claims 800MPa+)? The original website that indicated 0.8 tf for shearing m10 a4 gave 2.3 tf for m10 a4-80, which seemed just about enough (given that some load is also taken by the forward 2no mountings as well). And my second question is whether you pro engineers think I am seeing this right.
THanks!
JOsh
Confession first: I am not an engineering professional----so I realise that my question may get moderated away before it even sees the light of day! But if so I'm not sure where to take it ......
I am the owner of the 1911 Bristol Channel pilot cuter Cornubia. Now sailing Victorian or Edwardian workboats without winches, just with block-and-tackle, is knackering, and I decided that rather than have everyone pre-knackered before they even start sailing by raising the anchor on a manual windlass I would buy an electric one. Lofrans Falkon seemed to look reasonably timeless, and is a suitable size for 31tonne vessel, and we are just installing it now. What rather took me aback was that it is fixed with 4no ~11mm mounting holes (I think 7/16"), with plastic liners taking the size down to 10mm. GIven that the weight is borne primarily by the aft mountings this means that two m10 bolts are doing most of the work ...
This just seemed wrong, and indeed a quick check on some website gave the breaking load in shear of a4 m10 bolts (or maybe set screws) of around 0.8 tonne-force. (Obviously bolts have to be marine grade)
To put this in context, I've seen rule-of-thumb indications that anchor rode strength should be about 25% of boat weight, and this ties in with the ~7-8 tonne-force strength of our 12mm hot-dip galv chain; now it's very poor practice to leave the load on the windlass when anchored (you transfer it to a strong point on the boat), but 2no 0.8tonne-force still seemed very low.
POssibilities I considered were
1)Use some form of HT bolt: A4-80, 1.4462 duplex, 17-4ph, 8.8 hot-dip galv, 10.9 hot dip galv. I couldn't find 17-4ph or 10.9 hot-dip galv off the shelf; and 8.8 hot-dip galv didn't seem to have that much over a4-80 (both have tensile strength >800MPa) , so material choice came down to A4-80 or 1.4462 duplex.
2)Use 7/16 UNC or better still UNF bolts---but this would have meant removing the plastic liners (risking galvanic corrosion) and/or enlarging the holes (but the flanges didn't seem that huge to start with, and I worried about weakening the structure). Obviously I could have enlarged further (eg m12) but this was have magnified my concerns further ... so I decided to stick with m10.
So the eventual decision was to use M10 bolts (not set screws) in a4-80 or 1.4462; but web research showed that 1.4462 has strength ~650-850MPa, and a4-80 is advertised as 800 MPa+. So my first question is what justifies the huge expense (comparatively) of 1.4462 if it's weaker than a4-80 (claims 800MPa+)? The original website that indicated 0.8 tf for shearing m10 a4 gave 2.3 tf for m10 a4-80, which seemed just about enough (given that some load is also taken by the forward 2no mountings as well). And my second question is whether you pro engineers think I am seeing this right.
THanks!
JOsh
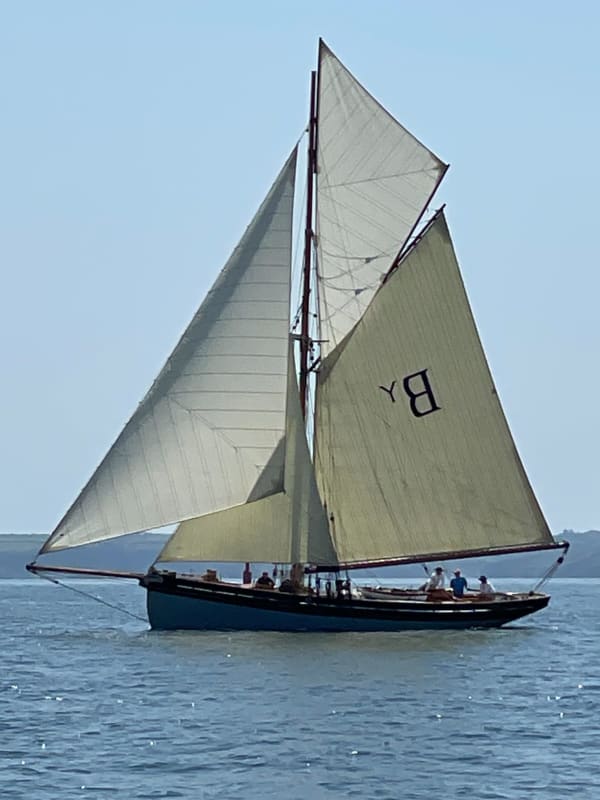