greenimi
Mechanical
- Nov 30, 2011
- 2,391
What is the best way to take advantage of datum feature shift offered by A(M)-B(M) callouts.
(Software Calypso version 2014 5.8.2 service pack 5)
See attachment ISO 5459:2011 for A-B concept (shown RMB per ASME Y14.5 terminology)
I would like to know how A(M)-B(M) is calculated and how to use this datum feature shift?
(Software Calypso version 2014 5.8.2 service pack 5)
See attachment ISO 5459:2011 for A-B concept (shown RMB per ASME Y14.5 terminology)
I would like to know how A(M)-B(M) is calculated and how to use this datum feature shift?
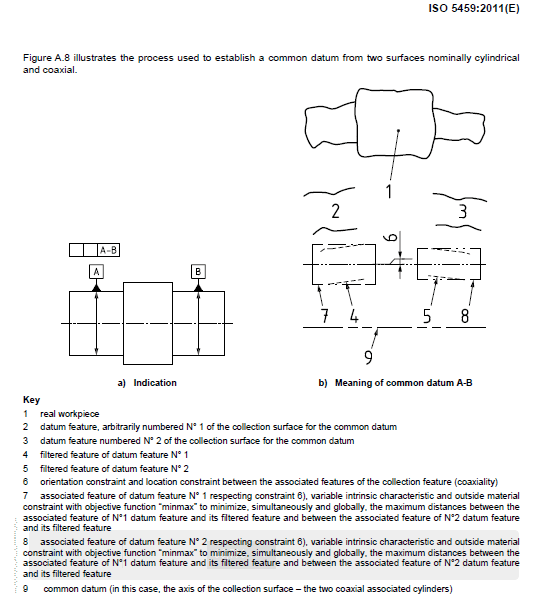