SeasonLee
Mechanical
- Sep 15, 2008
- 918
I have some questions about this print, and I tried to make some changes as shown below. The reasons for making these changes are:
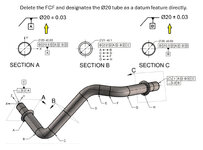
Do you agree with the changes on the datum callout? Please correct me if I am wrong here.
Thanks for your help.
Season
- The common datum(A-B) is constructed after the individual feature is designated as the datum feature.
- The existing DRF refers to the datum feature itself, normally we will consider it as a coaxial part, but here is a multiple skewed cylinder.
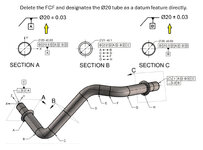
Do you agree with the changes on the datum callout? Please correct me if I am wrong here.
Thanks for your help.
Season
Last edited: