StructuralCivilFEA
Civil/Environmental
I am trying to see if my element has correct behavior in tension and compression. I have made a one element which is encastred at one side and elongated at the other.
I get the following tension behavior:
.
Which seems okay if I compare too abaqus documentation on CDPM, besides that the force seems to increase slightly at the end.
Then I try in compression and get this:
Why does the force keep increasing at the end? I have attached the CAE, any help would be appreciated as Ive been stuck for a while.
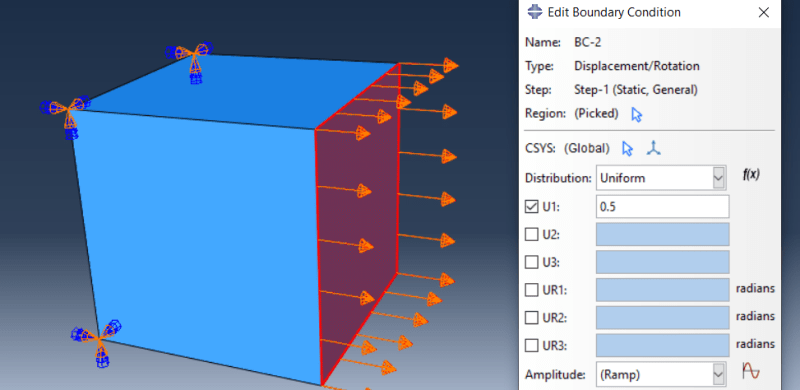
I get the following tension behavior:
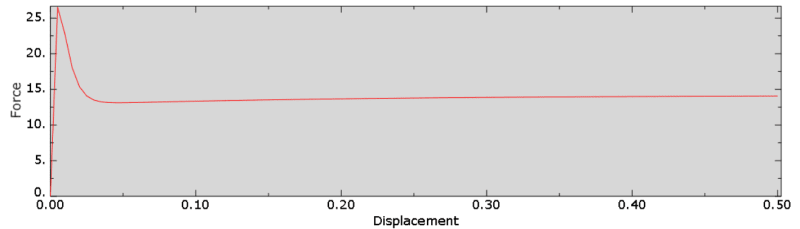
Which seems okay if I compare too abaqus documentation on CDPM, besides that the force seems to increase slightly at the end.
Then I try in compression and get this:
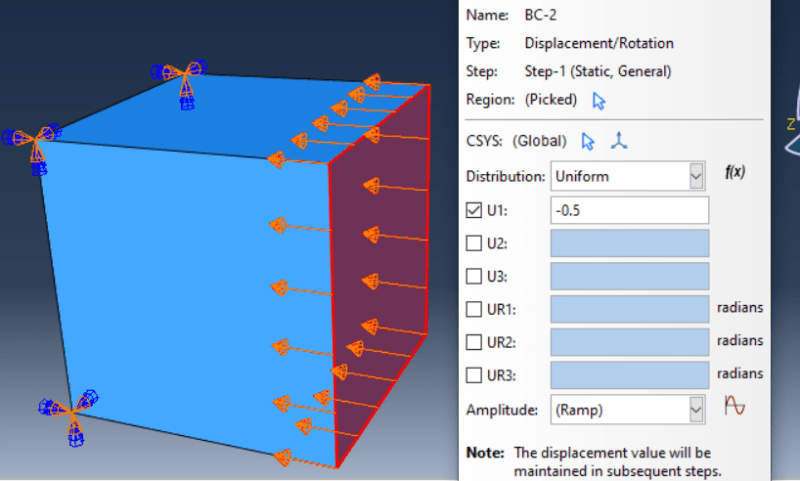
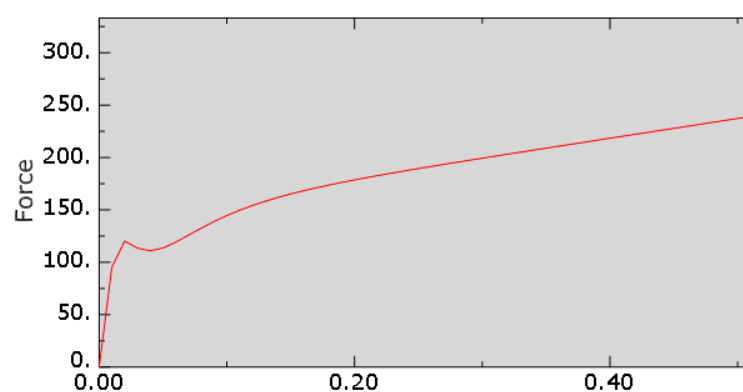
Why does the force keep increasing at the end? I have attached the CAE, any help would be appreciated as Ive been stuck for a while.