Ajith Kurian Baby
Mechanical
I was trying to simulate a wear problem with mesh motion subroutine. the job ran for 1 increment after which it aborted with an error. I refined mesh with coarse size but still showing error. please help me to rectify this issue.
The executable standard.exe aborted with system error code 1073741819. Please check the .dat, .msg, and .sta files for error messages if the files exist. If there are no error messages and you cannot resolve the problem, please run the command "abaqus job=support information=support" to report and save your system information. Use the same command to run Abaqus that you used when the problem occurred. Please contact your local Abaqus support office and send them the input file, the file support.log which you just created, the executable name, and the error code.
The executable standard.exe aborted with system error code 1073741819. Please check the .dat, .msg, and .sta files for error messages if the files exist. If there are no error messages and you cannot resolve the problem, please run the command "abaqus job=support information=support" to report and save your system information. Use the same command to run Abaqus that you used when the problem occurred. Please contact your local Abaqus support office and send them the input file, the file support.log which you just created, the executable name, and the error code.
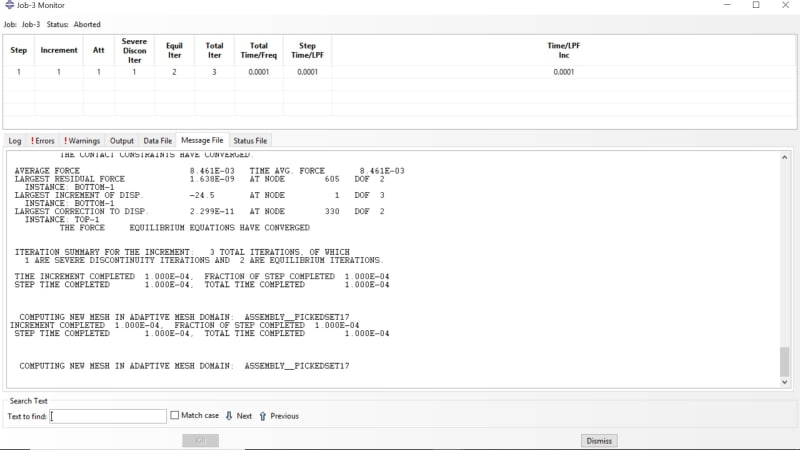