I don't know if there is a better place to address my issue but I thought I would start here.
I need to add two more attachment points or "ears' to a plastic material on a cab of a tractor. Since the manufacturer did not properly space the bolts that attach an access cover to the cab, the thin plastic access cover ~0.01 inches thick bows substantially between the bolts which are spaced 16.5 inches apart, as a result of the pressure of the sealing gasket which then creates a sealing issue. The plastic material at the front of the access hole is 0.150 inches and the plastic thickness at the rear of the access hole is 0.137 inches thick. See attachments.
NOTE:I tried to upload several photos and a drawing but in the preview, it only shows one attachment, the last.) After posting, I found out that only the last attachment was attached so I will try to attach the photos. I found out I cannot add any more attachments! I will try the image function above.
What is a feasible way to do this? Try to form a piece of metal to conform to the area at the edge of the hole which would be difficult and cement it to the plastic for an additional attachment point or perhaps there is better way.
Thanks
I need to add two more attachment points or "ears' to a plastic material on a cab of a tractor. Since the manufacturer did not properly space the bolts that attach an access cover to the cab, the thin plastic access cover ~0.01 inches thick bows substantially between the bolts which are spaced 16.5 inches apart, as a result of the pressure of the sealing gasket which then creates a sealing issue. The plastic material at the front of the access hole is 0.150 inches and the plastic thickness at the rear of the access hole is 0.137 inches thick. See attachments.
NOTE:I tried to upload several photos and a drawing but in the preview, it only shows one attachment, the last.) After posting, I found out that only the last attachment was attached so I will try to attach the photos. I found out I cannot add any more attachments! I will try the image function above.
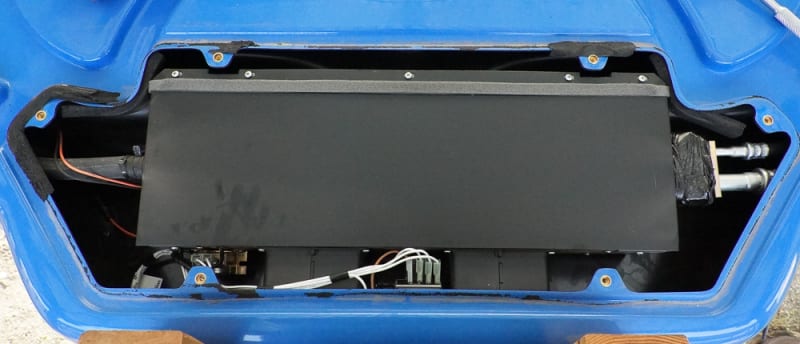
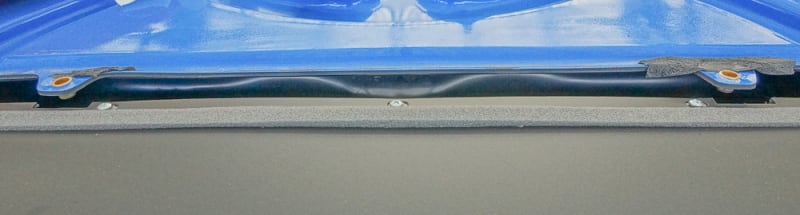

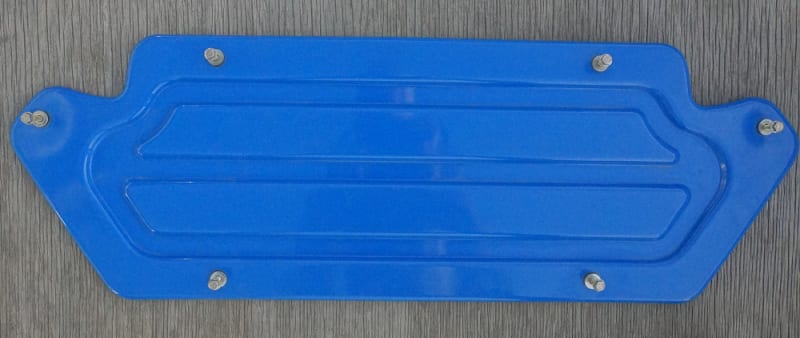
What is a feasible way to do this? Try to form a piece of metal to conform to the area at the edge of the hole which would be difficult and cement it to the plastic for an additional attachment point or perhaps there is better way.
Thanks