aniiben
Mechanical
- May 9, 2017
- 158
If the objective is to calculate the minimum distance then why 2.15 maximum is value SHOWN has to do with the correct answer.
As far as I understood the correct answer for minimum distance is: 0.15.
The maximum X distance is 2.85. Then what 2.15 is good for? What is the meaning of 2.15 value?
As far as I understood the correct answer for minimum distance is: 0.15.
The maximum X distance is 2.85. Then what 2.15 is good for? What is the meaning of 2.15 value?
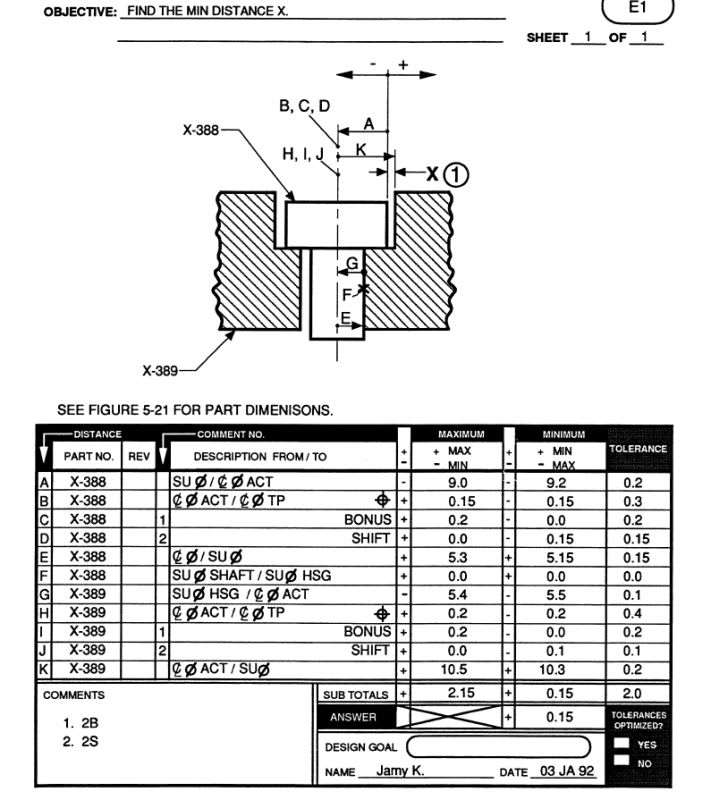
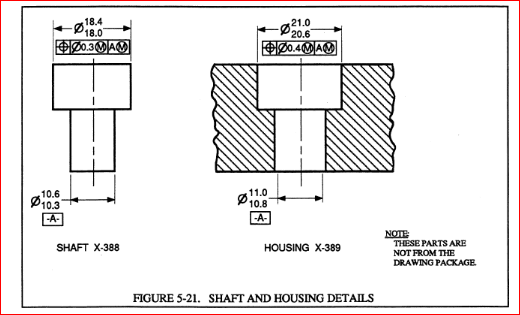