Amateur question. I have been bending my practice weld coupons around a small pipe, then bending tighter in a vice - just to check ductility.
Photos below are pre-bend and post-bend
Background:
Uphill, 3G
One-sided complete joint pen at butt joint (no gap)
6061, 1/8" thick
3/32" 5356 filler (roughly 2" of filler per 1" of weld)
3/32" tungsten with 16 to 17 cfh Argon, gas lens
About 115 amps, 75% electrode negative on Syncrowave
Most welds had full burnthru
No pulsing, relatively steady foot pedal, moderate SS wire brush cleaning prior
Coupons cut to approx 1" wide strips x 5" long
Some welds show very high ductility, but occasionally a weld fractures right at the heat affected zone ("HAZ"), without too much tension straining. Brittle.
I keep preparing to take my 3G test for AWS D1.2, but this is humbling. I would like to determine what are possible contributors. I'm not just the observer - I did the welding - very little difference between the welds - from prep to last puddle.
Any advice is welcome - but especially guys with lots of aluminum experience.
Photos below are pre-bend and post-bend
Background:
Uphill, 3G
One-sided complete joint pen at butt joint (no gap)
6061, 1/8" thick
3/32" 5356 filler (roughly 2" of filler per 1" of weld)
3/32" tungsten with 16 to 17 cfh Argon, gas lens
About 115 amps, 75% electrode negative on Syncrowave
Most welds had full burnthru
No pulsing, relatively steady foot pedal, moderate SS wire brush cleaning prior
Coupons cut to approx 1" wide strips x 5" long
Some welds show very high ductility, but occasionally a weld fractures right at the heat affected zone ("HAZ"), without too much tension straining. Brittle.
I keep preparing to take my 3G test for AWS D1.2, but this is humbling. I would like to determine what are possible contributors. I'm not just the observer - I did the welding - very little difference between the welds - from prep to last puddle.
Any advice is welcome - but especially guys with lots of aluminum experience.
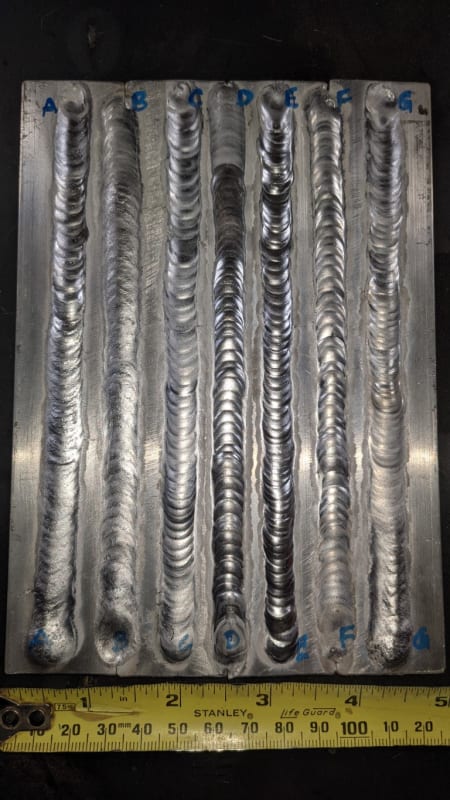
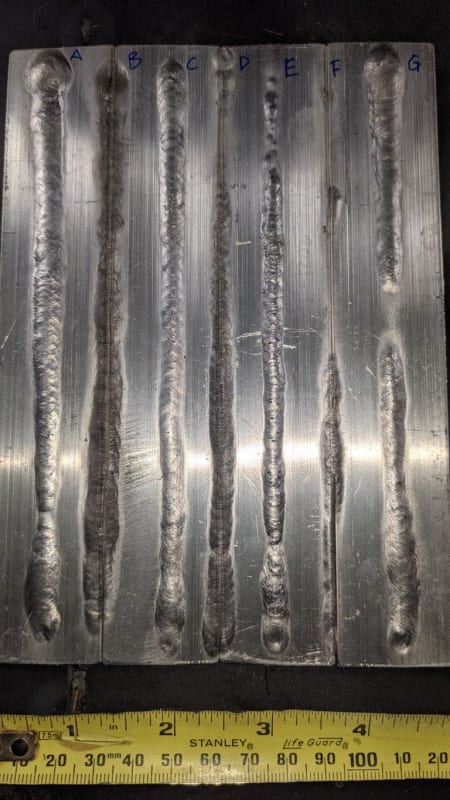
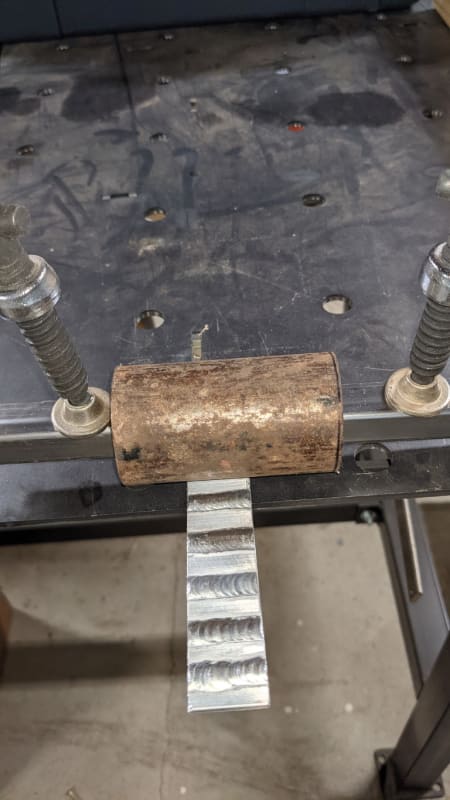
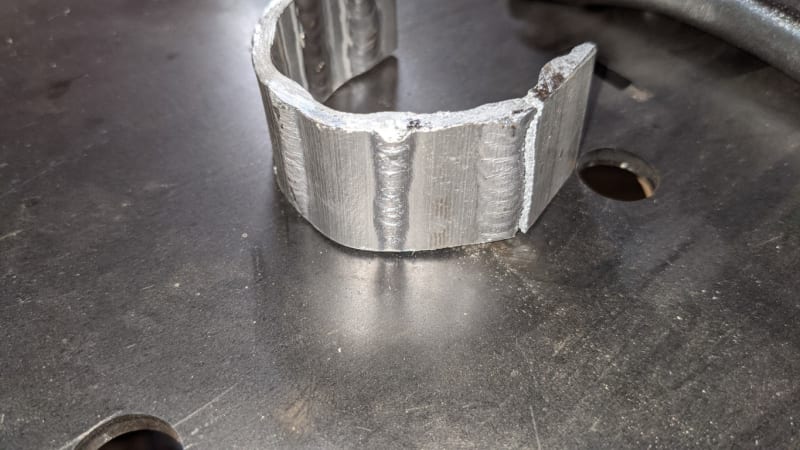