Hi.
Looking at the fixing of an 2mm aluminium cladding system to face of a building. The system is understood to have the detailing to allow for expansion and contraction of the panel. My engagement was specifying the fixing of the brackets to the wall.
However, in one zone, the wood framed walls were not constructed per plans. The cladding installer is asking to direct fix the top of the 5' tall by 2' wide panel (25lb) to the wall. The sides and bottom of the panel are free to expand and contract. The top and bottom are restrained in and out of plane. The proposed fixing detail would be 10mm dia hole in the aluminium panel, with a rubber washer in hole with 10Ga screw (5mm) through the center of hole and washer. It would theoretically allow for 2.5mm expansion and 2.5mm contraction at the top.
What to you think? If the panel is allowed to expand and contract on 3 of 4 sides, can other side (top) be restrained from thermal expansion? Considering durability (normal environment) and performance, what type of rubber washer would you recommend?
Looking at the fixing of an 2mm aluminium cladding system to face of a building. The system is understood to have the detailing to allow for expansion and contraction of the panel. My engagement was specifying the fixing of the brackets to the wall.
However, in one zone, the wood framed walls were not constructed per plans. The cladding installer is asking to direct fix the top of the 5' tall by 2' wide panel (25lb) to the wall. The sides and bottom of the panel are free to expand and contract. The top and bottom are restrained in and out of plane. The proposed fixing detail would be 10mm dia hole in the aluminium panel, with a rubber washer in hole with 10Ga screw (5mm) through the center of hole and washer. It would theoretically allow for 2.5mm expansion and 2.5mm contraction at the top.
What to you think? If the panel is allowed to expand and contract on 3 of 4 sides, can other side (top) be restrained from thermal expansion? Considering durability (normal environment) and performance, what type of rubber washer would you recommend?
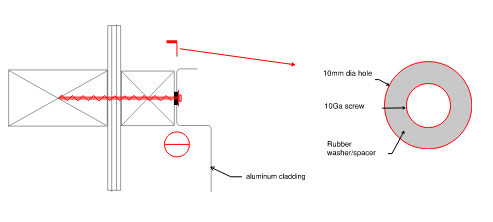