I am evaluating an steel anchor chair design for a ground supported water tank using AISI T-192 (per AWWA D100). Within AISI T-192, it states if chair height calculated is excessive, a solution maybe to use a continuous ring at the top of the chairs. Minimizing the eccentricity is not possible and the load on the anchors for the chair attachment are pretty high (130 kips) so I am having trouble keeping the localized stresses below the recommended maximum of 25ksi. So it appears using a continuous ring would help reduce the localized stresses transmitted to the shell.
The AISI document states to check for the maximum stress in the circumferential direction (assuming they mean hoop stress), considering the ring as though it were loaded with equally spaced concentrated loads equal to P*eccentricity/chair height.
My question is to evaluate the stresses in the ring:
1. Is the intention that the equally space concentrated loads are applied at each anchor chair around the shell?
2. Is there a formula to calculate the maximum stress in circumferential direction? I know how to calculate the hoop stress using a uniform loading but not sure how to for concentrated loads. Would using Roarks formulas for rings be applicable?
3. I assume I would need to add the hoop stress from hydrostatic load from inside the tank?
If anyone has any similar examples, it would be greatly appreciated.
The AISI document states to check for the maximum stress in the circumferential direction (assuming they mean hoop stress), considering the ring as though it were loaded with equally spaced concentrated loads equal to P*eccentricity/chair height.
My question is to evaluate the stresses in the ring:
1. Is the intention that the equally space concentrated loads are applied at each anchor chair around the shell?
2. Is there a formula to calculate the maximum stress in circumferential direction? I know how to calculate the hoop stress using a uniform loading but not sure how to for concentrated loads. Would using Roarks formulas for rings be applicable?
3. I assume I would need to add the hoop stress from hydrostatic load from inside the tank?
If anyone has any similar examples, it would be greatly appreciated.
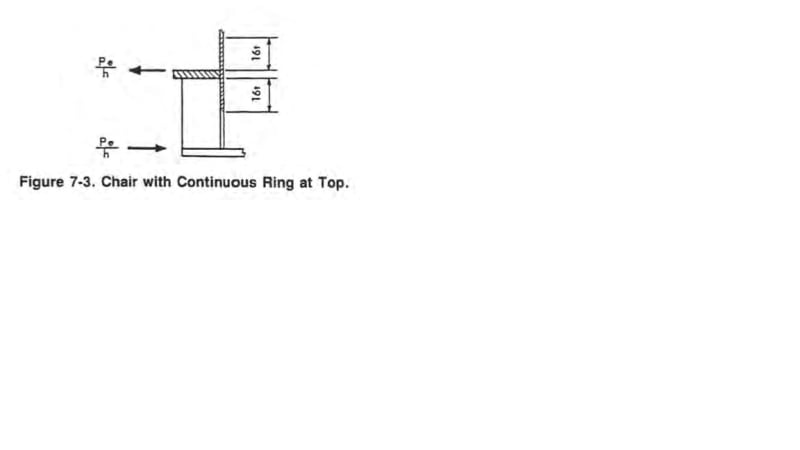