Ingenuity
Structural
- May 17, 2001
- 2,373
Last week Saturday there was a sizeable concrete placement close to a project I am working on - more than 700 cy - and being nosy I decided to swing by and take a look.
RC foundation slab with thickened edge beams for a new industrial warehouse lease complex by a local developer, who has many adjacent buildings of the same type (tin-can framing etc).
Anyway, interesting thing I noticed was that there were no anchor rods/bolts cast into the foundation for the steel frames of the PEMB. I went back on Monday and asked one of the workers why they did not install anchor rods, and he informed me that they 'always drill them after, as the frame columns are installed'.
Is this now the typical procedure for installing anchor rods for PEMB's?
RC foundation slab with thickened edge beams for a new industrial warehouse lease complex by a local developer, who has many adjacent buildings of the same type (tin-can framing etc).
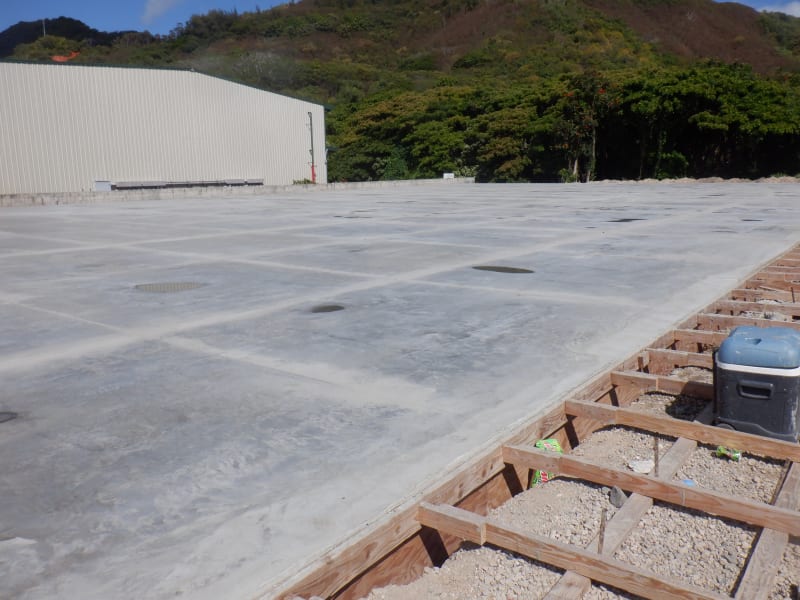
Anyway, interesting thing I noticed was that there were no anchor rods/bolts cast into the foundation for the steel frames of the PEMB. I went back on Monday and asked one of the workers why they did not install anchor rods, and he informed me that they 'always drill them after, as the frame columns are installed'.
Is this now the typical procedure for installing anchor rods for PEMB's?