Dear gents,
I did design calculation for oil storage tank based on API650 (Annex F)
Input data:
Tank’s internal diameter = 34m
Design internal pressure P= 12 kPa
Roof slope 6:1
Material: ASTM A 516 GR. 70
I calculated A (Required Compression Area, Roof/Shell Junction Area as per Section F.5) for frangible roof case and got 60404 mm^2!!!
The initial idea was to make a tank with frangible roof. There is a limitation for Frangible Roof-to-Shell Junction Area Limit which cannot be exceeded (see 5.10.2.6 API650)
Frangible Roof-to-Shell Junction Area Limit is A= 8913.7 mm^2
Because Required Compression Area 60404 mm^2 is much more than Frangible Roof-to-Shell Junction Area Limit 8913.7 mm^2 frangible roof design cannot be used.
I go to non-frangible roof design and attach roof plates to the rafters and girders by welding.
The total required compression area at the roof-to-shell junction is be calculated as per API650 F.5.1 and is reduced equal to A= 58 552 mm^2
I checked all the API650 if there is any Limit for non-frangible tank’s roof designed but there is no such limitation. For your understanding initially I planned to use angle L NPL150 with dimensions 150x150mm and thickness 15mm. But Net Area at Roof/Shell Junction including 3mm Corrosion allowance would be 6660 mm^2 only and shall be increased in 10 times to pass the calculation of required compression area at the roof-to-shell junction.
So my idea is to find The biggest top angle available on the market or to weld from plates any customized angle to get required compression area at the roof-to-shell junction 58 552 mm^2.
The biggest angle which I found was equal L angle 305mmx305mm x 35mm.But even this giant super angle has 19355 mm^2 area only (and it will be reduced for CA!)
Is there any Limit for compression area at the roof-to-shell junction for non-frangible roof?
Is there any solution how to design tank 34m in diameter and 12 kPa internal pressure?
I did design calculation for oil storage tank based on API650 (Annex F)
Input data:
Tank’s internal diameter = 34m
Design internal pressure P= 12 kPa
Roof slope 6:1
Material: ASTM A 516 GR. 70
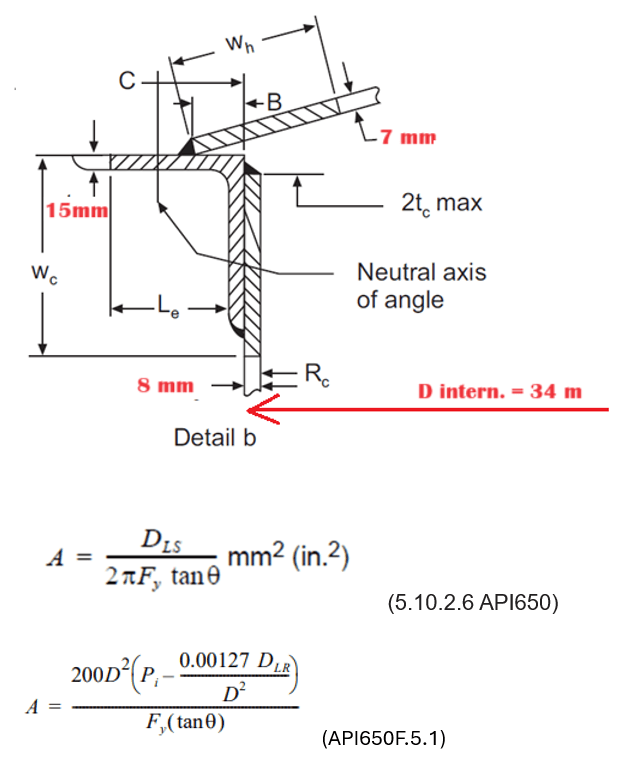
I calculated A (Required Compression Area, Roof/Shell Junction Area as per Section F.5) for frangible roof case and got 60404 mm^2!!!
The initial idea was to make a tank with frangible roof. There is a limitation for Frangible Roof-to-Shell Junction Area Limit which cannot be exceeded (see 5.10.2.6 API650)
Frangible Roof-to-Shell Junction Area Limit is A= 8913.7 mm^2
Because Required Compression Area 60404 mm^2 is much more than Frangible Roof-to-Shell Junction Area Limit 8913.7 mm^2 frangible roof design cannot be used.
I go to non-frangible roof design and attach roof plates to the rafters and girders by welding.
The total required compression area at the roof-to-shell junction is be calculated as per API650 F.5.1 and is reduced equal to A= 58 552 mm^2
I checked all the API650 if there is any Limit for non-frangible tank’s roof designed but there is no such limitation. For your understanding initially I planned to use angle L NPL150 with dimensions 150x150mm and thickness 15mm. But Net Area at Roof/Shell Junction including 3mm Corrosion allowance would be 6660 mm^2 only and shall be increased in 10 times to pass the calculation of required compression area at the roof-to-shell junction.
So my idea is to find The biggest top angle available on the market or to weld from plates any customized angle to get required compression area at the roof-to-shell junction 58 552 mm^2.
The biggest angle which I found was equal L angle 305mmx305mm x 35mm.But even this giant super angle has 19355 mm^2 area only (and it will be reduced for CA!)
Is there any Limit for compression area at the roof-to-shell junction for non-frangible roof?
Is there any solution how to design tank 34m in diameter and 12 kPa internal pressure?