MechEng0001
Mechanical
We have a large 200 tonne catamaran-style dredge that we are planning to tow with a couple of D11 dozers up a hill. We are designing a platform that it will sit on and be lashed down to, and this is what the dozers will be attached to using towing strops. This platform will have a large welded beam across the front of it, however, I need to establish the how the loads are being applied to it so we can size the beam in our beam calculators.
In the attached sketch, we have assumed that the dozers may stop and start, so the entire force from one may be applied to a single side at any one time. We have also assumed that the structure of the dredge cannot/will not take any of the load through it. We have assumed this because we don't know if the structure is strong enough to handle these loads. So, essentially we have two pontoons acting independently. I figured we could assume a point load where the centre of mass is in these pontoons, which is essentially the reaction forces. However, this could also be a distributed mass as the skid plate will be connected along two lengths of the beam, I'm not 100% sure. If point loading is a worst case scenario and makes the calcs simpler, we are happy to assume that. The link below is an Excel file showing how I calculated the reaction forces from the moments.
Beam Calcs
Now, technically the beam will move when the required force is applied. This is problematic for beam calculators as it's not constrained. I have done a force balance calculation to find the reaction forces from the location of the pontoon CoGs and modelled these as forces. There is some residual force/moment at the end of the beam, which was required to be added into the model as a fixed joint to constrain everything, however this is negligible.
So me question is, is this the correct way to set up this beam analysis? Are my assumptions reasonable? Something just feels off about it and it doesn't fill me with confidence. Any input would be appreciated.
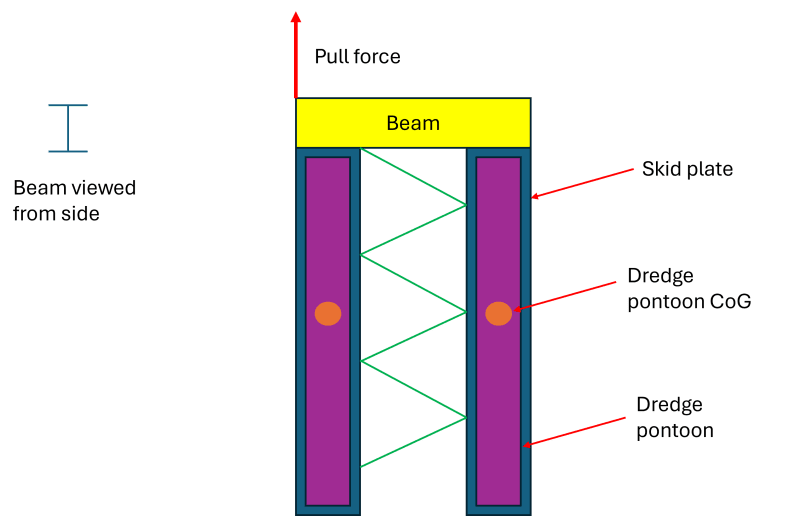
In the attached sketch, we have assumed that the dozers may stop and start, so the entire force from one may be applied to a single side at any one time. We have also assumed that the structure of the dredge cannot/will not take any of the load through it. We have assumed this because we don't know if the structure is strong enough to handle these loads. So, essentially we have two pontoons acting independently. I figured we could assume a point load where the centre of mass is in these pontoons, which is essentially the reaction forces. However, this could also be a distributed mass as the skid plate will be connected along two lengths of the beam, I'm not 100% sure. If point loading is a worst case scenario and makes the calcs simpler, we are happy to assume that. The link below is an Excel file showing how I calculated the reaction forces from the moments.
Beam Calcs
Now, technically the beam will move when the required force is applied. This is problematic for beam calculators as it's not constrained. I have done a force balance calculation to find the reaction forces from the location of the pontoon CoGs and modelled these as forces. There is some residual force/moment at the end of the beam, which was required to be added into the model as a fixed joint to constrain everything, however this is negligible.
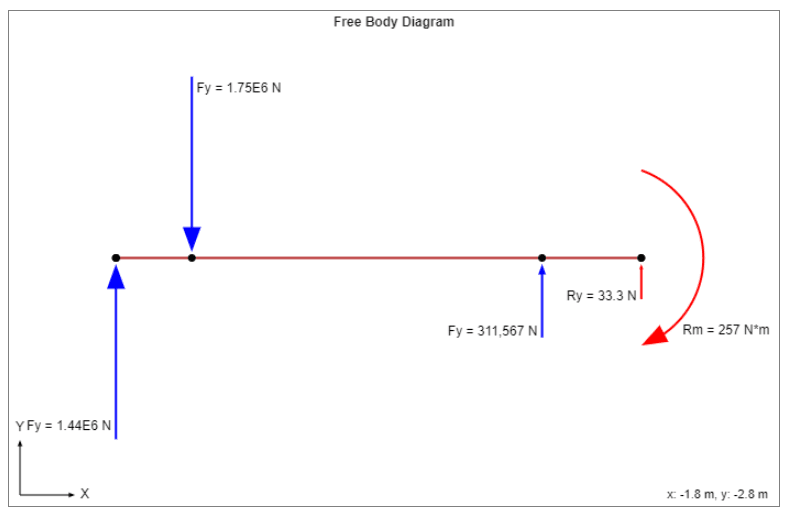
So me question is, is this the correct way to set up this beam analysis? Are my assumptions reasonable? Something just feels off about it and it doesn't fill me with confidence. Any input would be appreciated.