Good day All,
In regards flange thickness (tf as per ASME B16.5), I always refer to Table 8 for class 150#. But without clear explanation, now one of the new vendor had delivered us as per table 9, picture below.
Gate valve 1/2" Class 150#, material is WCB, measured upon arrival tf is 8,6 mm. Whereas table 8 should have minimum of 9.6 mm. And manufacturer without any technical justification refer to table 9 with minimum 8 mm.
I do read the notes on (1),(2) and (4) on both table. It is bit grey area the definition of integrated flange (read: fitting).
Did some simple calculation using flange stress analysis. Gasket used is spiral wound gasket
with minimum 9.6 mm, it would requires 64 Nm to tighten the 4 bolts. Maximum 97 Nm prior jeopardizing the flange ring structure.
With 8.6 mm, it would requires maximum 44 Nm to tighten the bolts, before the integrity of the flange's 'ring' is start to be compromised. This torque value quite on the low side and not as per our flange management standard. I've seen bent spiral wound outer ring upon tightening, but never really see bent flange ring.
I will reject the valve, but aside from above stress calculation, does it really justified with respect to ASME B16.5 for them to use table 9? So far this is the only counter argument from the manufacturer.
Kindly advise,
Thank you in advance,
Regards,
MR
All valves will last for years, except the ones that were poorly manufactured; are still wrongly operated and or were wrongly selected
In regards flange thickness (tf as per ASME B16.5), I always refer to Table 8 for class 150#. But without clear explanation, now one of the new vendor had delivered us as per table 9, picture below.
Gate valve 1/2" Class 150#, material is WCB, measured upon arrival tf is 8,6 mm. Whereas table 8 should have minimum of 9.6 mm. And manufacturer without any technical justification refer to table 9 with minimum 8 mm.
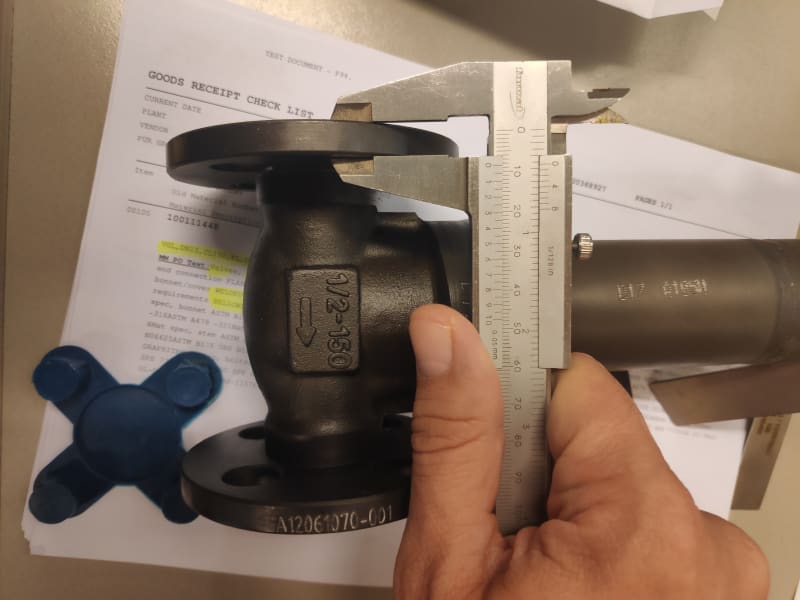
I do read the notes on (1),(2) and (4) on both table. It is bit grey area the definition of integrated flange (read: fitting).
Did some simple calculation using flange stress analysis. Gasket used is spiral wound gasket
with minimum 9.6 mm, it would requires 64 Nm to tighten the 4 bolts. Maximum 97 Nm prior jeopardizing the flange ring structure.
With 8.6 mm, it would requires maximum 44 Nm to tighten the bolts, before the integrity of the flange's 'ring' is start to be compromised. This torque value quite on the low side and not as per our flange management standard. I've seen bent spiral wound outer ring upon tightening, but never really see bent flange ring.
I will reject the valve, but aside from above stress calculation, does it really justified with respect to ASME B16.5 for them to use table 9? So far this is the only counter argument from the manufacturer.
Kindly advise,
Thank you in advance,
Regards,
MR
All valves will last for years, except the ones that were poorly manufactured; are still wrongly operated and or were wrongly selected